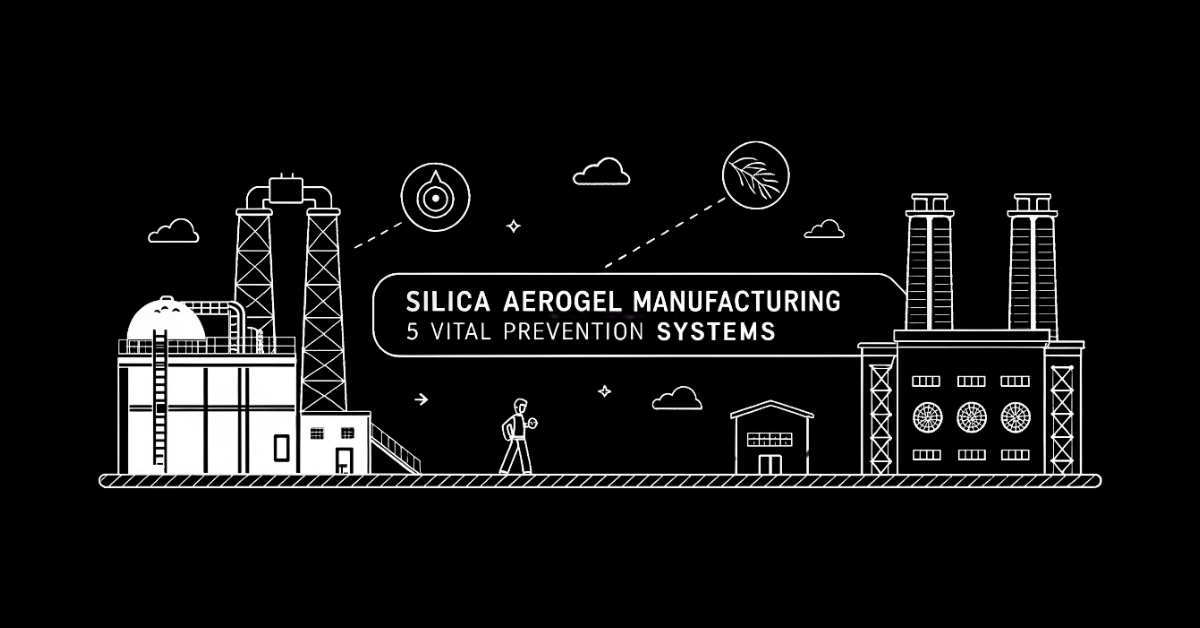
Most aerogel production fails.
Projects collapse. Batches vary wildly. Promising research stalls at commercialization. The best insulation material in the world stays trapped in a cycle of inconsistent manufacturing.
Silica aerogels are amazing – they insulate better than almost anything while weighing almost nothing. But making them consistently has frustrated researchers and manufacturers for years. The gap between what aerogels could do and what they actually deliver comes down to processes that keep failing.
At Aerogel Machinery, we’ve built systems that fix these problems. This article covers the five critical systems that prevent common failures in silica aerogel manufacturing.
Table of Contents
The Main Challenges in Silica Aerogel Manufacturing
Silica aerogels are among the lightest solid materials you can make. They have a porous structure that’s more than 90% air. This makes them perfect for everything from building insulation to spacecraft parts.
But making them consistently is hard. Traditional methods run into:
- Quality issues between batches
- Variations that hurt performance
- Production failures that waste materials and money
The core problem is the complex chemistry. Making aerogels demands precision at every step—from mixing chemicals through drying. However, industrial production of aerogels is so far mostly limited to silica-based systems, limiting the possibility to prove the potential application by prototyping (source).
Why Normal Production Methods Don’t Work
The sol-gel process that creates silica aerogels involves two key chemical reactions:
- Hydrolysis: A silica precursor reacts with water to form silanol groups
- Condensation: These silanol groups connect to create the 3D network
Keeping these chemical conditions stable gets harder as you scale up. Things you can control in a lab become much harder to manage in a factory.
The drying stage causes the most problems. Bad drying destroys the aerogel structure—turning what should be a light material into a dense, cracked product with none of the properties you want.
Moving from lab to factory introduces quality control challenges that standard equipment just can’t handle.
System #1: Advanced Process Control Technology
According to our knowledge and years of experience, reliable aerogel production starts with precision control systems that eliminate batch-to-batch variation that ruins conventional manufacturing approaches.
These systems provide automated monitoring throughout manufacturing, keeping quality consistent from initial mixing through final drying. Instead of occasional manual checks, modern technology watches and adjusts critical parameters continuously.
Advanced control enables real-time adjustments based on how the material behaves during critical production phases. Each batch gets optimized treatment based on its specific characteristics, rather than following rigid steps that ignore batch differences.
How Digital Control Makes Aerogel Consistent
The sol-gel process needs precise control of multiple factors at once. Process variables like pH, temperature, and pressure must be constantly monitored and kept within narrow ranges.
Behind this are control algorithms that prevent problems that would otherwise ruin products. These algorithms don’t just maintain fixed conditions—they anticipate and respond to the changing nature of chemical reactions happening during aerogel formation.
The result is consistency from batch to batch. Manufacturers can count on predictable properties and performance, eliminating the quality variations that have made silica aerogel manufacturing so challenging.
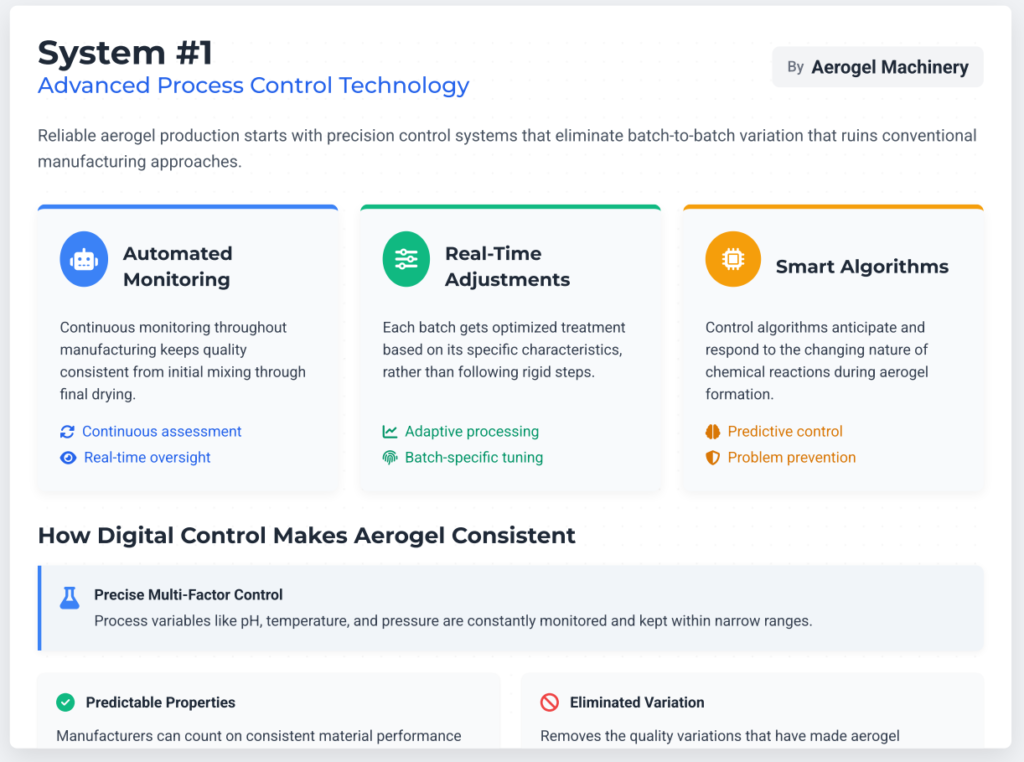
System #2: Specialized Drying Equipment Suite
Drying is the most critical phase in aerogel production—and where most failures happen with standard equipment. As one of the major suppliers for Aerogel Machinery, we offers a complete range of drying equipment options that transform this weak point into a strength.
Custom-engineered supercritical drying systems optimized for specific aerogel formulations ensure reliable results. Rather than using general equipment adapted from other industries, purpose-built drying systems address the unique demands of silica aerogel manufacturing.
These specialized systems are designed specifically to prevent the collapse of the porous network during solvent removal—the most common cause of production failures.
The Critical Role of Supercritical Drying
Supercritical drying is a specialized process that eliminates surface tension and capillary forces that typically cause structural collapse during drying. This approach preserves the porosity and low density that make aerogels valuable.
In this process, the wet gel must be carefully heated and pressurized above the critical point of the solvent, creating conditions where there is no distinct liquid-gas boundary. Properly designed equipment ensures precise control of these conditions, maintaining the delicate balance needed for successful drying (source).
Without proper equipment design, this phase becomes a production bottleneck with high failure rates. Specialized drying systems transform this vulnerable stage into a reliable, consistent process that preserves the essential characteristics of the aerogel structure.
System #3: Sol-Gel Preparation Systems
The foundation of successful aerogel production begins with the initial chemical reactions that form the nanoporous gel network. When you are looking for the solutions to produce aerogel, you nee to look for specialized equipment for precisely controlling these crucial early stages to ensure quality from the start.
Sol-gel preparation systems are designed to ensure proper formation of silanol (Si–OH) groups and siloxane (Si–O–Si) bonds—the fundamental chemical structures that determine aerogel quality. By controlling these reactions from the beginning, manufacturers establish the foundation for consistent, high-quality production.
These systems incorporate consistent mixing and reaction apparatus that deliver reproducible results batch after batch. From magnetic stirrers and heating mantles to precisely controlled reaction vessels, every component is engineered to support silica aerogel manufacturing chemistry.
Ensuring Chemical Precision at Every Scale
One of the biggest challenges in aerogel manufacturing is maintaining consistent chemical processes as production scales increase. Our study shows that Aerogel Machinery’s modern systems provide the same level of precision whether working with laboratory-scale systems as small as 1L or industrial systems up to 2000L capacity.
This scalability ensures a seamless transition between research and production. Formulations developed in the laboratory can be reliably reproduced at industrial scale without the reformulation and process adjustments typically required when scaling up production.
The result is a dramatic reduction in development time and resources. Manufacturers can focus on optimizing their aerogel formulations rather than struggling with the process inconsistencies that typically emerge during scale-up.
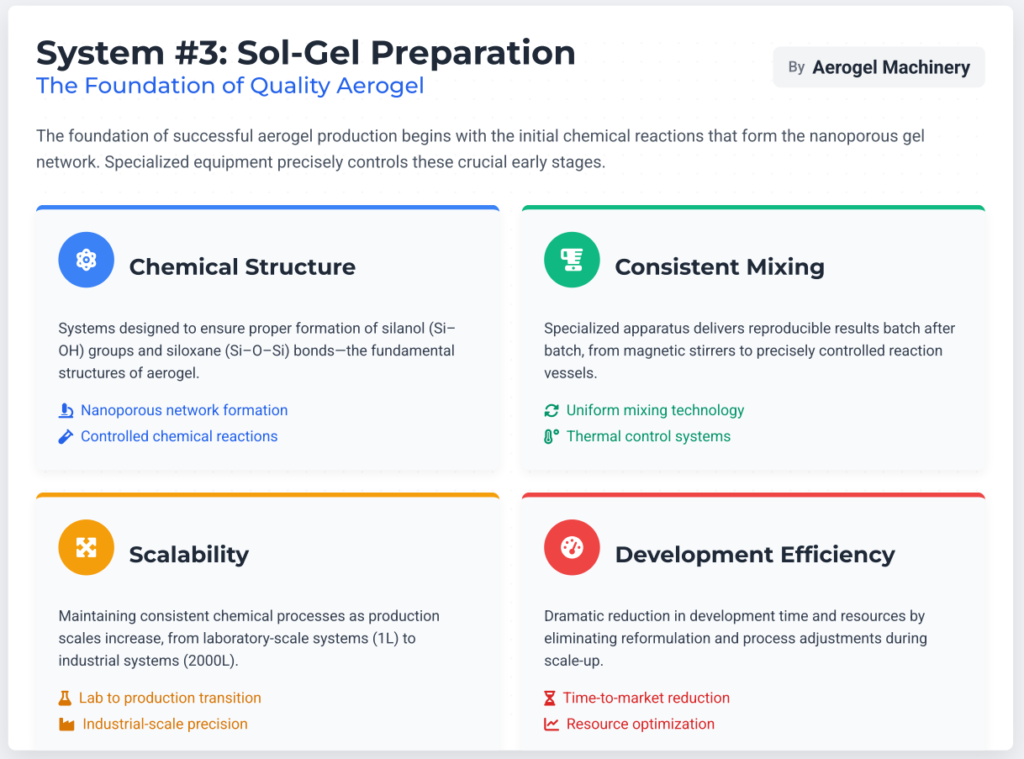
System #4: Energy Recovery and Optimization Systems
Energy management represents a critical but often overlooked aspect of reliable silica aerogel manufacturing. The heat recovery systems like ours improve energy efficiency while maintaining process integrity.
These systems provide optimized thermal management that prevents energy-related process variations. By maintaining stable thermal conditions throughout production, manufacturers avoid the temperature fluctuations that can compromise aerogel quality.
Beyond stability, properly designed equipment fine-tunes processes for maximum yield, quality, and energy efficiency. This optimization reduces production costs while simultaneously improving product consistency—a win-win approach that enhances manufacturing economics.
Energy recovery systems also contribute to more sustainable manufacturing practices. By capturing and reusing thermal energy that would otherwise be wasted, these systems reduce the environmental footprint of aerogel production while improving economic performance.
System #5: Integrated Production Lines
While individual system components each play crucial roles, their integration into a cohesive production line ultimately determines manufacturing success. Suppliers like us provides complete end-to-end manufacturing solutions that eliminate interface issues between process steps.
These integrated solutions prevent the knowledge gaps that typically lead to manufacturing failures. Rather than piecing together equipment from different suppliers with varying specifications and control systems, an integrated approach ensures seamless communication and coordination throughout the production process.
Each system component is engineered to work harmoniously with others, preventing the cascading failures that often occur when process steps are misaligned. This holistic approach transforms silica aerogel manufacturing from a sequence of vulnerable operations to a robust, reliable manufacturing process.
The 4-Step Methodology That Ensures Success
Behind integrated production lines lies a systematic 4-step methodology that guides implementation and ensures manufacturing success. Here at Aerogel Machinery, we follows this approach:
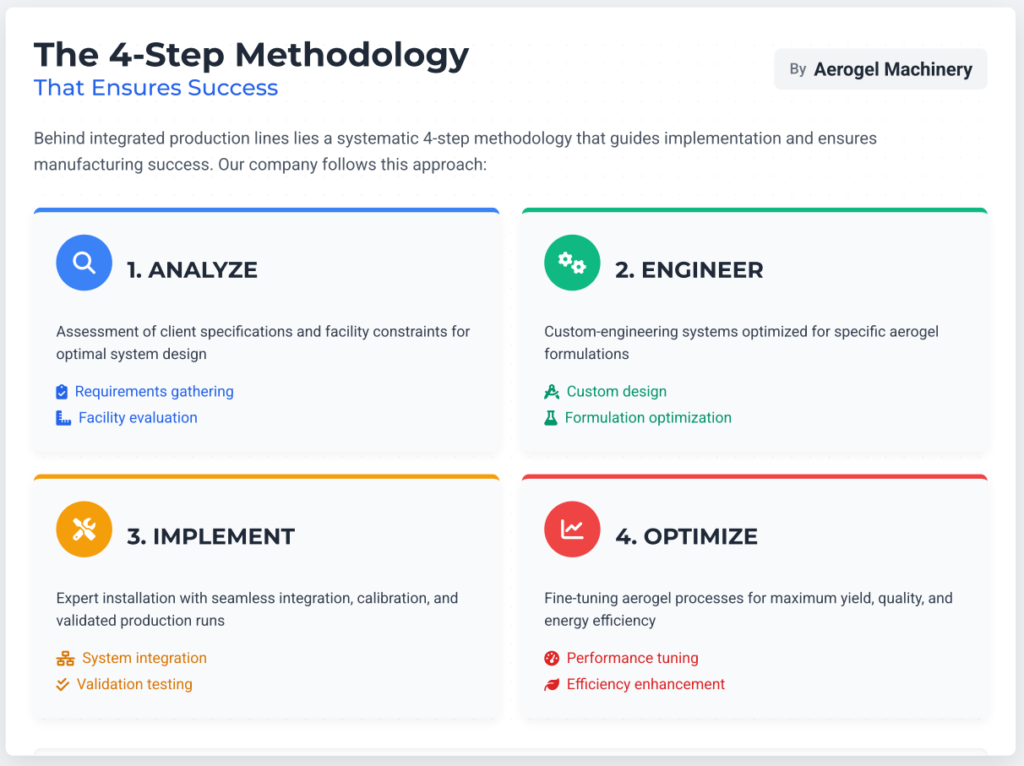
This structured approach eliminates the trial-and-error implementation that characterizes conventional aerogel production, replacing it with a methodical process that consistently delivers results.
Applications Driving the Need for Reliable Aerogel Production
The demand for consistent, high-quality aerogel manufacturing systems is driven by the expanding range of applications for these remarkable materials. For instance:
- Thermal insulation for aerospace, construction, and industrial applications represents one of the largest markets
- Energy storage applications, including carbon-based aerogels for batteries and capacitors, require precise control of aerogel properties
- Advanced composites and specialty materials present additional requirements for batch-to-batch consistency
These demanding applications highlight why reliable production systems have become essential for manufacturers seeking to capitalize on the unique properties of aerogels.
Conclusion: The Future of Failure-Free Aerogel Manufacturing
Technical excellence in equipment design is transforming what’s possible in aerogel production. The systems described in this article represent a fundamental shift in manufacturing capability, replacing unpredictable processes with reliable, consistent production.
Knowledge transfer ensures production teams master the complex process of aerogel production. Beyond equipment, comprehensive documentation prevents the manufacturing knowledge gaps that have traditionally limited successful implementation.
Continuous optimization remains the key to advancing aerogel manufacturing technology. As production processes evolve and new applications emerge, ongoing refinement of manufacturing methods will continue to improve both quality and economics.
At Aerogel Machinery, we’re committed to making the remarkable properties accessible through reliable, consistent silica aerogel manufacturing. If you’re struggling with the limitations of conventional production methods or seeking to scale up laboratory successes to industrial production, we invite you to explore how our specialized equipment can transform your aerogel manufacturing capability.
Leave a Reply