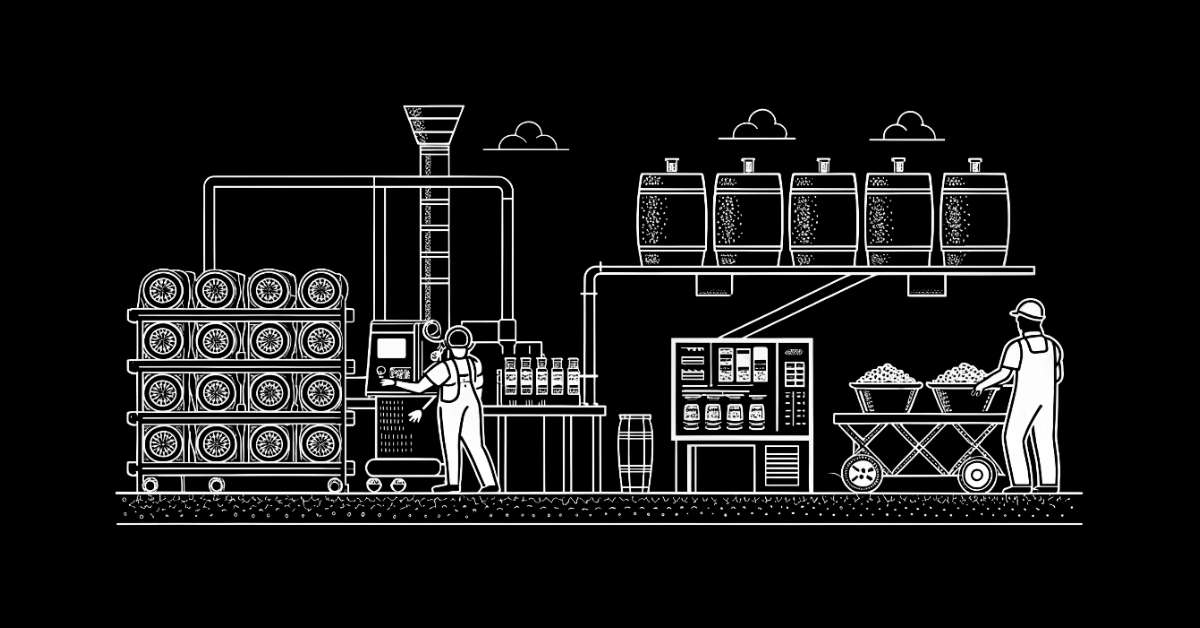
Imagine a material so light it feels like holding a cloud, yet strong enough to insulate spacecraft. That’s aerogel. An aerogel production line allows you to create this extraordinary material for industries like construction, aerospace, and energy storage. Its significance lies in its ability to produce high-performance insulation and other advanced materials efficiently.
Demand for aerogels is skyrocketing. Recent analysis shows a growing interest in aerogel fibers for diverse applications, reflecting this surge. With the right tools and guidance, setting up your own production line becomes not just possible but practical. You can turn a complex process into a manageable and rewarding venture.
Key Takeaways
- Aerogel production lines combine specialized equipment for creating ultra-lightweight insulation materials with exceptional thermal properties.
- Setting up a production facility requires careful planning, proper equipment selection, and adherence to safety protocols for optimal manufacturing results.
- Quality machinery and materials are critical success factors that directly impact aerogel performance and production efficiency.
- Safety protocols must be prioritized throughout the production process to protect personnel and ensure consistent product quality.
- Regular maintenance of production equipment prevents costly downtime and maintains manufacturing consistency.
- Market research helps align your production capabilities with industry demands for maximum commercial success.
- Aerogel Machinery LLC provides comprehensive solutions from equipment selection to installation, research support, and production optimization.
- Starting with small-scale production allows for process refinement before scaling to industrial manufacturing volumes.
Table of Contents
Understanding Aerogels
What Are Aerogels?
Definition and Unique Properties of Aerogels
Aerogels are extraordinary materials known for their ultra-lightweight structure and exceptional insulating properties. They are created by replacing the liquid in a gel with gas, resulting in a solid material that is over 90% air. This unique composition gives aerogels their remarkable strength-to-weight ratio and thermal insulation capabilities.
Unlike traditional materials, aerogels minimize heat transfer through convection, conduction, and radiation. This makes them highly effective for applications requiring superior insulation. For example, studies show that aerogel insulation can save homeowners up to $750 annually on energy bills. Their versatility and performance make them a cornerstone of modern material science.
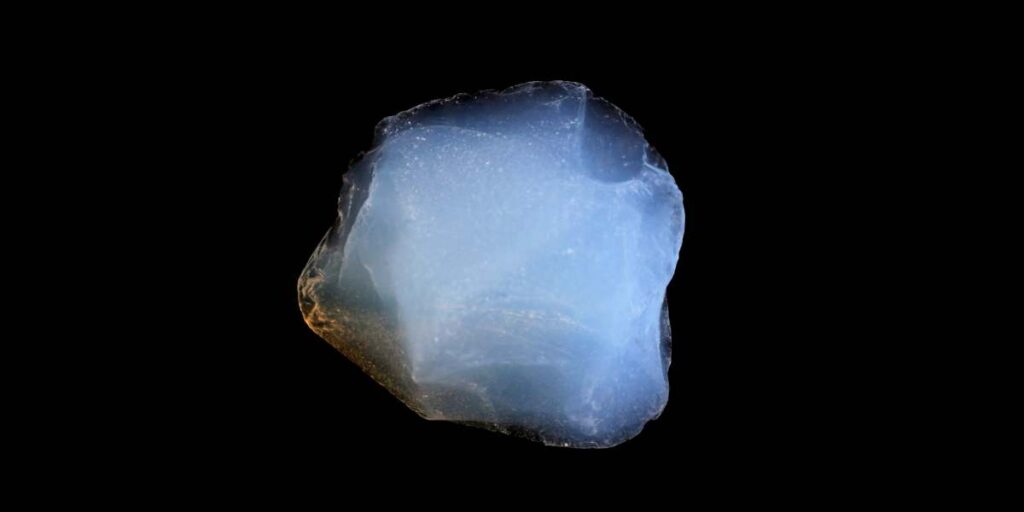
Types of Aerogels and Their Manufacturing Requirements
Different types of aerogels require specific production line configurations:
- Silica Aerogels: The most common type, requiring precise drying equipment in the production line for thermal insulation and lightweight structural components.
- Carbon Aerogels: Need specialized carbonization systems within the production line. Known for their electrical conductivity, these are used for energy storage devices like batteries and supercapacitors.
- Polymer-Based Aerogels: Require controlled polymerization equipment in the manufacturing setup, offering flexibility and durability for advanced composites.
Each aerogel type demands specific equipment configurations and process parameters in your aerogel manufacturing line. Understanding these requirements is essential for designing an efficient production system.
Applications of Aerogels
Commercial Uses: Insulation, Aerospace, and Energy Storage
Aerogels have revolutionized several industries with their unmatched performance. In construction, they provide superior thermal insulation, outperforming traditional materials like fiberglass and polyurethane foam. The table below highlights how aerogels compare to other insulation materials:
Material Type | Thermal Conductivity (W/m·K) | Durability in High Humidity | Lifespan (Years) | Cost Comparison (per m²) |
---|---|---|---|---|
Aerogel | 0.013–0.018 | >95% of insulating properties | 15–20 | 3–5x fiberglass |
Fiberglass | 0.030–0.040 | Loses up to 40% R-value | 8–12 | N/A |
Polyurethane Foam | 0.022–0.035 | N/A | N/A | N/A |
In aerospace, aerogels are used to insulate spacecraft and protect sensitive equipment from extreme temperatures. Their lightweight nature reduces payload weight, saving costs and improving efficiency. Carbon aerogels, on the other hand, play a critical role in energy storage, enhancing the performance of batteries and capacitors.
Research Applications Requiring Specialized Production Systems
In research settings, aerogels are invaluable for studying advanced materials and their properties. Their unique structure allows scientists to explore new possibilities in nanotechnology, catalysis, and environmental science. Polymer-based aerogels, for instance, are being developed for use in water purification and oil spill cleanup.
Laboratory-scale aerogel production lines allow researchers to experiment with new formulations and process parameters. These smaller systems serve as proving grounds for innovations that can later be scaled to industrial production.
If you’re considering setting up an aerogel production line, these applications highlight the vast potential of aerogels in both commercial and scientific domains. By understanding their properties and uses, you can better align your production goals with market demands.
Essential Equipment for High-Performance Aerogel Production Lines

Setting up an aerogel production line requires the right combination of equipment and materials. Each component plays a critical role in ensuring efficiency, quality, and scalability. Let’s break down the essentials you’ll need to get started.
Core Production Machinery
Reactors and Autoclaves for Sol-Gel Processing
Reactors and autoclaves form the backbone of your aerogel manufacturing system. These tools handle the sol-gel process, where liquid precursors transform into a gel. Reactors allow precise control over temperature, pressure, and mixing, ensuring consistent gel formation. Autoclaves, on the other hand, are essential for high-pressure processes like supercritical drying. Without these, achieving the desired aerogel properties becomes nearly impossible.
Industrial-grade reactors for aerogel production typically feature:
- Temperature control within ±0.5°C for precise reaction management
- Advanced mixing systems to ensure homogeneous gel formation
- Automated monitoring systems for consistent quality control
- Scalable capacities from 1L (laboratory) to 2000L (industrial production)
Drying Systems, Including Supercritical and Alternative Drying Methods
Drying systems are where the magic happens in an aerogel production plant. Supercritical drying is the gold standard for producing high-quality aerogels. It replaces the liquid in the gel with gas, preserving the material’s porous structure. While energy-intensive, this method ensures superior insulation performance. Alternative drying methods, such as ambient pressure drying, offer cost-effective solutions for specific applications. Choosing the right system depends on your production goals and budget.
Key features of industrial drying systems include:
- Pressure vessels rated for 8-15 MPa for supercritical operation
- CO₂ recovery systems for cost reduction and environmental compliance
- Automated cycling for consistent batch processing
- Safety interlocks and redundant controls for operator protection
Mixing and Stirring Tools for Material Preparation
Before the sol-gel process begins, you’ll need reliable mixing and stirring tools. These ensure uniform distribution of precursors, catalysts, and additives. High-shear mixers are particularly effective for achieving homogeneity in the mixture. Proper mixing minimizes defects and enhances the overall quality of your aerogels.
Advanced preparation equipment in modern production lines includes:
- High-precision dosing systems for exact chemical ratios
- Vacuum degassing units to eliminate bubbles and inconsistencies
- Temperature-controlled vessels to manage reaction kinetics
- Filtration systems to remove contaminants for pure aerogel products
Raw Materials and Supply Chain Management
Precursors Like Silica, Resorcinol, and Carbon Sources
The choice of raw materials directly impacts the quality and cost of your aerogels. Silica is the most common precursor, ideal for thermal insulation. Resorcinol and carbon sources are used for specialized applications like energy storage. However, variations in material density can lead to waste during production. Standardizing your raw materials helps reduce inefficiencies and maintain consistentquality.
- Silica aerogels often require supercritical drying, which increases production costs.
- Density variations in raw materials can result in material waste.
- Future trends suggest innovations in recycling could lower costs over time.
Solvents and Catalysts: Selection for Optimal Production Flow
Solvents and catalysts are crucial for initiating the sol-gel reaction. Additives like trimethylchlorosilane (TMCS) are used to make aerogels hydrophobic, enhancing their durability in humid environments. Proper handling and storage of these chemicals ensure safety and efficiency in your production line.
An efficient aerogel production line requires a strategic approach to raw material management:
- Implementing just-in-time inventory systems to reduce storage costs
- Establishing relationships with multiple suppliers to mitigate supply chain risks
- Creating standardized quality control protocols for incoming materials
- Developing recycling processes for solvents to reduce operational costs
Finishing and Processing Equipment
Cutting and Shaping Technology for Commercial Aerogel Products
Once your aerogels are ready, cutting and shaping tools help customize them for various applications. Precision cutting machines ensure minimal waste and consistent product dimensions. These specialized tools transform raw aerogel blocks into market-ready products with exact specifications.
Packaging Solutions for Aerogel Market Distribution
Packaging tools, such as vacuum sealers, protect your aerogels during storage and transportation. Efficient packaging also enhances the commercial appeal of your products. The right packaging solution preserves product integrity while optimizing shipping costs and storage requirements.
Pro Tip: Investing in advanced tools for by-product manufacturing can significantly boost efficiency. For example, techniques like SMED (Single-Minute Exchange of Dies) reduce changeover times, allowing you to produce smaller batches more frequently.
Aerogel Machinery LLC’s Comprehensive Equipment Solutions
You might think setting up an aerogel production line ends with core equipment like reactors and drying systems. But what about the final steps—cutting, shaping, and packaging your aerogel products? These steps are just as critical for ensuring your products meet market demands. Without the right tools, you risk inefficiencies, wasted materials, and inconsistent product quality.
Aerogel Machinery LLC understands this challenge. That’s why we go beyond supplying core equipment for raw material processing. We also provide specialized machinery for the finishing stages of production. This ensures your aerogels are not only high-quality but also market-ready.
Some of our market-ready solutions include:
- Aerogel Blanket Production Lines: Complete automated systems for manufacturing fiber-reinforced aerogel composites, including fiber substrate preparation, sol-gel impregnation, and continuous processing equipment.
- Ultra-Fine Grinding Mills: Precision cryogenic grinding systems that reduce aerogel particles to ultra-fine powder (1-45μm) while preserving their nanostructure. Ideal for laboratory applications and specialized industrial processes requiring high-purity aerogel additives.
- Hot Press Machines: Specialized thermal compression systems designed specifically for aerogel materials, featuring precise temperature control (up to 800°C) and uniform pressure distribution. Essential for manufacturing composite panels and densified aerogel products.
- Die Cutting Equipment: Advanced precision cutting systems specifically designed for delicate aerogel materials, including rotary die cutters for high-volume production and flatbed systems for complex geometries. Our equipment ensures clean edges without material compression or damage.
- Hydrophobization Treatment Units: Specialized equipment for surface modification of aerogel materials to enhance water resistance and long-term performance.
- Automated Packaging Systems: Custom-designed packaging lines that preserve aerogel integrity during handling and transportation, featuring dust containment, precision sizing, and protective packaging options.
By partnering with Aerogel Machinery LLC, you gain access to a holistic equipment solution that covers every aspect of aerogel production, from raw material processing to advanced product development. This integrated approach eliminates compatibility issues and optimizes your entire product-to-market process.
Did You Know? Aerogel Machinery’s integrated equipment systems can reduce production time by up to 30% compared to piecing together equipment from multiple vendors.
Are you ready to take your aerogel production line to the next level? Equip yourself with the tools that guarantee success. Aerogel Machinery has everything you need to produce, refine, and package world-class aerogels.
Comprehensive Setup Process for an Aerogel Production Line

Production Facility Planning
Selecting a Suitable Location: Laboratory or Industrial Space
Your workspace sets the foundation for your aerogel production line. Choosing the right location ensures smooth operations and compliance with industry standards. For laboratory-scale production, opt for a controlled environment with minimal external disturbances. Industrial-scale setups require larger spaces with adequate room for equipment and workflow optimization.
Consider proximity to utilities like water, electricity, and ventilation systems. A well-connected location reduces operational delays and enhances efficiency. Ask yourself: Does your chosen space accommodate future expansion? Planning ahead saves time and costs when scaling up production.
Key facility requirements for an optimal aerogel production line include:
- Minimum ceiling height of 5-7 meters for vertical equipment installation
- Reinforced flooring (capable of supporting 1000-1500 kg/m²) for heavy machinery
- Separate zones for chemical handling, production, and packaging
- Adequate power supply (typically 3-phase industrial power) for equipment operation
- Proper drainage systems for process waste management
Installing Ventilation, Safety Systems, and Energy-Efficient Setups
Ventilation is critical for handling solvents and catalysts safely. Install exhaust systems to maintain air quality and prevent chemical exposure. Safety systems, such as fire suppression units and emergency shutoffs, protect your workspace and personnel.
Energy-efficient setups reduce operational costs and environmental impact. Use LED lighting and energy recovery systems to optimize power consumption. These measures not only lower expenses but also align your production line with sustainability goals.
An industrial aerogel production facility should incorporate:
- Explosion-proof electrical installations in areas handling flammable solvents
- Negative pressure ventilation systems to prevent chemical vapor spread
- Emergency shower and eyewash stations at strategic locations
- Heat recovery systems to capture and reuse thermal energy from drying processes
- Smart monitoring systems for tracking energy consumption and identifying efficiency opportunities
Positioning Reactors, Autoclaves, and Drying Systems
Proper equipment placement minimizes workflow disruptions. Position reactors and autoclaves near mixing stations for seamless sol-gel preparation. Drying systems should be installed in areas with controlled temperature and humidity to ensure consistent aerogel quality.
A well-designed aerogel production line layout considers:
- Process flow optimization to minimize material transport distances
- Equipment accessibility for maintenance and repair operations
- Logical progression from raw material handling to finished product
- Buffer zones between critical process steps to prevent bottlenecks
- Future expansion possibilities without major reconstruction
Aerogel Machinery offers on-site services to design and install your workspace efficiently. Our experts analyze your facility layout and recommend optimal equipment positioning. This service eliminates guesswork and ensures your production line operates smoothly from day one.
Process Control and Heat Recovery Systems Implementation
Process control systems monitor temperature, pressure, and reaction times. These systems ensure precision, reducing errors and improving aerogel consistency. Heat recovery systems capture excess energy and reuse it, lowering operational costs.
Calibration plays a vital role in maintaining equipment accuracy. Industries like aerospace and automotive rely on regular calibration to meet strict tolerances and reduce defects. Benefits include:
- Quality Assurance: Precise calibration ensures compliance with industry standards.
- Cost Savings: Reduces material waste and rework, lowering production costs.
- Efficiency Improvement: Minimizes downtime caused by equipment failures.
Starting the Production Process
Sol-Gel Preparation and Gelation Process Control
The sol-gel process begins with mixing precursors, solvents, and catalysts. Use high-shear mixers to achieve uniform distribution. Initiate gelation by controlling temperature and pH levels. This step determines the structural integrity of your aerogels.
Consistency is key in an efficient aerogel production line. Variations in the sol-gel mixture can lead to defects in the final product. Follow standardized procedures to ensure reliable results.
Advanced process parameters to monitor include:
- Precise pH control (typically ±0.1 units) during gelation
- Temperature stability within ±1°C throughout the aging process
- Controlled aging times to optimize pore structure development
- Mixing speeds calibrated to prevent air entrapment while ensuring homogeneity
Supercritical and Alternative Drying Techniques in Production
Drying transforms the gel into aerogel by removing liquid while preserving its porous structure. Supercritical drying is the preferred method for high-quality aerogels. It uses high pressure and temperature to replace liquid with gas, maintaining the material’s unique properties.
Alternative methods, like ambient pressure drying, offer cost-effective solutions for specific applications. Choose the drying method that aligns with your production goals and budget.
Industrial drying process optimization includes:
- Precise pressure and temperature ramp rates to prevent structural collapse
- Optimized solvent exchange procedures to minimize processing time
- Controlled depressurization rates to preserve nanopore structure
- Customized cycles for different aerogel formulations and applications
Aerogel Machinery LLC’s Comprehensive Support Services
Aerogel Machinery provides full-support for setting up your production line. Our team of experts offers:
- On-site installation services that ensure proper equipment setup and calibration
- Workspace design consultation to optimize flow and efficiency
- Process parameter development tailored to your specific production goals
- Staff training programs to ensure proper equipment operation and maintenance
Additionally, we offer valuable R&D and formula development services. Our experts help refine your processes and create market-ready products. This ensures your aerogels meet industry demands and stand out in the global marketspace.
Pro Tip: Collaborating with Aerogel Machinery gives you access to cutting-edge research and development. Our services optimize your production line for maximum efficiency and profitability.
Scaling Your Aerogel Production Line
From Laboratory to Commercial Production: Key Considerations
Transitioning from laboratory to commercial scale requires careful planning. Consider these factors when scaling your aerogel production line:
- Process consistency must be maintained across different production volumes
- Equipment scaling should follow a modular approach for gradual capacity increase
- Quality control systems need to adapt to higher throughput requirements
- Workflow optimization becomes critical for maintaining efficiency at larger scales
A successful scaling strategy incorporates:
- Pilot-scale testing before full commercial implementation
- Process parameter adjustments to accommodate larger batch sizes
- Equipment validation at each scaling stage
- Comprehensive staff training for larger operation management
Adapting Production Systems for Market-Specific Requirements
Different markets require customized production approaches. For construction applications, focus on large-volume production of insulation panels. Aerospace customers may require smaller batches with higher performance specifications.
Your aerogel manufacturing process should be flexible enough to accommodate these varying requirements:
- Modular production line design allows for quick reconfiguration
- Adjustable processing parameters accommodate different product specifications
- Multi-product capability increases market reach and production line utilization
- Batch tracking systems ensure quality consistency for demanding applications
Safety Measures and Best Practices in Aerogel Production
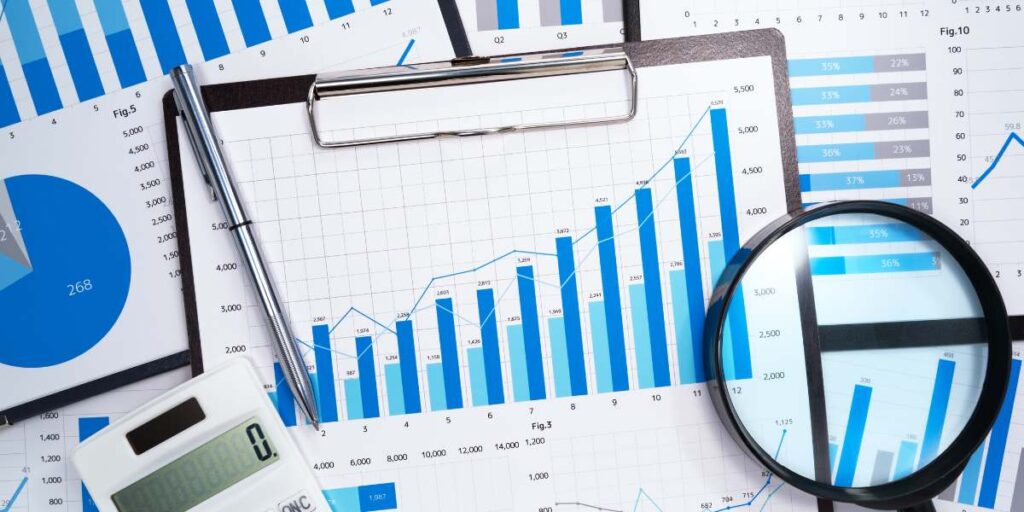
Safety is the backbone of any successful aerogel production line. Without it, even the most advanced equipment and processes can lead to costly mistakes or dangerous situations. By prioritizing safety, you not only protect your team but also ensure consistent, high-quality production.
Chemical Safety in Manufacturing Operations
Handling and Storage Systems for Production Materials
Handling chemicals like solvents and catalysts requires precision and care in an aerogel manufacturing facility. These substances can be volatile, flammable, or toxic. Always store them in designated, well-ventilated areas with proper labeling. Use chemical-resistant containers to prevent leaks or contamination.
When transferring chemicals, avoid spills by using tools like funnels or pumps. Keep incompatible substances, such as acids and bases, stored separately to prevent reactions. Ask yourself: Are your storage practices compliant with industry standards? Regular audits can help you identify and fix gaps.
Using Personal Protective Equipment (PPE) and Safety Protocols
Your first line of defense against chemical hazards is personal protective equipment (PPE). Equip yourself and your team with gloves, goggles, and lab coats. For high-risk tasks, use respirators or face shields. PPE minimizes exposure to harmful substances, reducing health risks.
Follow established safety protocols during every step of production. For example, always neutralize chemical spills immediately and dispose of waste according to local regulations. Training your team on these protocols ensures everyone knows how to respond to emergencies.
Pro Tip: Create a checklist for PPE and safety protocols. Review it daily to ensure compliance and reduce risks.
Equipment Safety for Production Lines
Operating High-Pressure Systems in Manufacturing Environments
Autoclaves and other high-pressure systems are essential for aerogel production, but they can be dangerous if mishandled. Always operate these systems within their specified pressure and temperature limits. Overloading or improper use can lead to equipment failure or accidents.
Before starting, inspect the autoclave for signs of wear or damage. Ensure all safety valves and pressure gauges are functioning correctly. During operation, monitor the system closely to detect any irregularities. A small oversight can escalate into a major issue.
Industrial aerogel production lines require:
- Automated pressure relief systems with redundant controls
- Regular certification of pressure vessels by qualified inspectors
- Operator training specific to high-pressure equipment
- Documented standard operating procedures for each equipment type
Preventive Maintenance Programs for Production Equipment
Routine maintenance keeps your equipment running smoothly and prevents unexpected breakdowns. Develop a maintenance schedule that includes cleaning, lubrication, and part replacements. Regular inspections help you identify minor issues before they become costly problems.
Evidence Type | Description |
---|---|
Demonstrating compliance | Inspection records prove compliance during safety audits, avoiding fines. |
Improved Safety | Frequent checks enhance workplace safety and reduce accident risks. |
Preventing Major Breakdowns | Inspections catch small issues early, ensuring smoother operations. |
A holistic maintenance strategy also relies on performance metrics. Track data like downtime, repair frequency, and energy consumption. Use this information to optimize your maintenance plan and improve efficiency.
Did You Know? Facilities with documented maintenance records experience 35% fewer equipment failures. Keeping detailed logs can save you time and money.
General Best Practices
Training Staff and Adhering to Industry Regulations
Your team is your greatest asset. Invest in regular training to ensure they understand the production process and safety protocols. Well-trained staff can identify potential hazards and respond effectively to emergencies.
Adhering to industry regulations is non-negotiable. Compliance not only protects your business from legal issues but also builds trust with clients and stakeholders. Stay updated on the latest standards and incorporate them into your operations.
Maintaining a Clean and Organized Workspace
A clean workspace is a safe workspace. Clutter increases the risk of accidents and slows down production. Organize your tools and materials to create a streamlined workflow. Use labeled storage bins and racks to keep everything in its place.
Regular cleaning prevents the buildup of dust and chemical residues, which can compromise product quality. Schedule daily or weekly cleaning sessions to maintain a safe and efficient environment.
Actionable Step: Implement the 5S methodology (Sort, Set in order, Shine, Standardize, Sustain) to keep your workspace organized and safe.
By following these safety measures and best practices, you create a production line that is not only efficient but also secure. Remember, safety is not just a requirement—it’s a commitment to excellence.
Common Challenges and Solutions in Setting Up an Aerogel Production Line
Every production line faces hurdles. Aerogel manufacturing is no exception. From technical glitches to scaling up operations, challenges can disrupt your workflow. But with the right strategies, you can overcome these obstacles and ensure smooth production.
Technical Challenges
Troubleshooting Equipment Malfunctions and Process Inefficiencies
Equipment malfunctions can halt production. Reactors may overheat, or autoclaves might fail to maintain pressure. These issues often stem from improper calibration or wear and tear. Regular maintenance is your best defense. Schedule inspections to identify potential problems early. Keep spare parts on hand to minimize downtime during repairs.
Process inefficiencies, like uneven gelation or drying inconsistencies, can affect product quality. Address these by standardizing procedures. Use automated process control systems to monitor variables like temperature and pressure. These systems reduce human error and improve consistency.
Tip: Train your team to recognize early signs of equipment failure. Quick action can prevent costly delays.
Ensuring Consistent Aerogel Quality Across Batches
Batch-to-batch variations can undermine your product’s reliability. Factors like raw material inconsistencies or improper mixing often cause these issues. To ensure uniformity, source high-quality precursors and standardize your sol-gel preparation process. High-shear mixers can help achieve a homogeneous mixture, reducing defects.
Quality control is essential. Test each batch for properties like density and thermal conductivity. Use data from these tests to refine your processes. Consistency builds trust with your customers and strengthens your market position.
Cost Management
Reducing Material Waste and Optimizing Energy Usage
Material waste increases costs. For example, excess silica or solvents can go unused during production. Optimize your material usage by implementing precise measurement systems. These systems ensure you use only what’s necessary, reducing waste.
Energy usage is another significant expense. Supercritical drying, while effective, consumes a lot of energy. Heat recovery systems can offset this by capturing and reusing excess heat. Switching to energy-efficient equipment also lowers operational costs.
Pro Tip: Monitor your energy consumption regularly. Small adjustments can lead to significant savings over time.
Sourcing Cost-Effective Feedstocks for Production
Raw materials like silica and resorcinol can be expensive. Finding cost-effective suppliers without compromising quality is crucial. Build relationships with multiple vendors to secure competitive pricing. Bulk purchasing can also reduce costs.
Innovative methods, like recycling waste materials, offer additional savings. For instance, some manufacturers repurpose by-products from other industries as feedstocks. Explore these options to lower your production costs further.
Meeting Increased Demand for Aerogels and By-Products
As demand grows, your production line must keep pace. This requires not only scaling up but also diversifying your product range. Insulation blankets, for example, are a high-demand by-product. Invest in specialized equipment to produce these efficiently.
Automation can also boost your output. Automated cutting and packaging systems streamline operations, reducing labor costs and increasing throughput. Monitor market trends to anticipate demand shifts and adjust your production accordingly.
Actionable Step: Use predictive analytics to forecast demand. This helps you plan production and avoid overstocking or shortages.
Scaling up may seem daunting, but with the right strategies, it becomes manageable. Focus on efficiency, quality, and adaptability to meet the growing needs of the aerogel market.
Implementing Your Aerogel Production Line: Next Steps

Key Success Factors for Commercial Manufacturing
Critical Production Line Elements for Market Competitiveness
Success in aerogel production begins with a solid foundation. Proper planning ensures your production line operates efficiently and meets market demands. Selecting the right equipment, such as reactors and drying systems, guarantees consistent quality. Safety measures protect your team and maintain smooth operations. Without these elements, even the most advanced processes can falter.
Think of your aerogel production line as a system where every component matters. From workspace design to chemical handling, each step contributes to the final product. By prioritizing these aspects, you set yourself up for long-term success.
Critical success factors include:
- Process reliability that ensures consistent batch quality
- Energy efficiency to manage operational costs
- Scalable equipment that grows with market demand
- Quality control systems that verify product performance
- Safety protocols that protect personnel and facilities
Potential for Commercial Success with Aerogels and Their By-Products
The aerogel market is expanding rapidly. This growth stems from advancements in manufacturing techniques and the rising demand for energy-efficient materials. Governments are incentivizing energy-efficient construction, making aerogels a preferred choice for building projects. Hybrid solutions that combine aerogels with traditional materials are also gaining traction, offering a balance between cost and performance.
North America leads the market due to strict energy regulations and green building practices. Meanwhile, the Asia-Pacific region is experiencing the fastest growth, with a projected annual growth rate of 25%. These trends highlight the immense potential for commercial success. By producing aerogels and their by-products, you can tap into a lucrative and evolving market.
Getting Started with Your Production Line
Practical Implementation Steps for Beginners
Starting your aerogel production journey may seem daunting, but breaking it into manageable steps makes it achievable. Begin by identifying your production goals. Are you focusing on insulation, energy storage, or advanced composites? Defining your niche helps you choose the right equipment and materials.
Next, invest in high-quality tools and raw materials. Reliable equipment minimizes errors and ensures consistent results. Partnering with experts, like Aerogel Machinery LLC, simplifies the setup process. Their comprehensive services, from workspace design to equipment installation, provide a seamless start.
Finally, prioritize safety and efficiency. Train your team on proper handling techniques and maintain a clean workspace. Regularly inspect your equipment to prevent malfunctions. These practices not only protect your investment but also enhance productivity.
Implementation sequence for a new aerogel production facility:
- Planning phase: Define production goals, space requirements, and budget
- Facility preparation: Ensure proper utilities, safety systems, and environmental controls
- Equipment installation: Set up and calibrate core production machinery
- Process validation: Test and refine production parameters with small batches
- Production scale-up: Gradually increase batch sizes while maintaining quality
- Market introduction: Begin commercial production and distribution
Pro Tip: Start small with a laboratory-scale setup. This allows you to refine your processes before scaling up to industrial production.
Support Resources from Aerogel Machinery LLC
Aerogel Machinery offers more than just equipment. We provide end-to-end support to ensure your success. Our post-sale services include on-site installation, process optimization, and formula development. These resources help you create market-ready products that meet industry standards.
Additionally, our expertise in scaling production ensures a smooth transition from small-scale to industrial operations. Whether you need guidance on equipment calibration or advice on market trends, our team is ready to assist. By partnering with Aerogel Machinery, you gain access to a wealth of knowledge and tools tailored to your needs.
Comprehensive support services include:
- Technical consultation for production line design and optimization
- Equipment selection guidance based on your specific requirements
- Installation and commissioning by experienced engineers
- Operator training programs for effective equipment utilization
- Ongoing technical support for troubleshooting and maintenance
- R&D collaboration for product development and improvement
Did You Know? Aerogel Machinery also offers R&D services to help you innovate and stay ahead in the competitive aerogel market.
Starting your aerogel production line is a journey filled with opportunities. With the right planning, tools, and support, you can turn your vision into reality. Are you ready to take the first step?
Aerogels represent a breakthrough in material science, offering great performance across industries like aerospace, construction, and energy storage. Their lightweight structure and exceptional insulation properties make them indispensable for applications requiring efficiency and sustainability. For example, the aerospace sector relies on aerogels to improve fuel efficiency and meet stringent regulations, while industries worldwide embrace them to reduce ecological impact.
Setting up an aerogel production line requires careful planning and attention to detail. From selecting the right equipment to ensuring safety and scalability, every step plays a role in your success. Advances in manufacturing technologies now make aerogel production more accessible, allowing you to meet growing market demands while maintaining high-quality standards.
The potential of aerogel production is immense. With the right tools and guidance, you can contribute to a market that values innovation and sustainability. Are you ready to explore this opportunity and make your mark in the world of advanced materials?
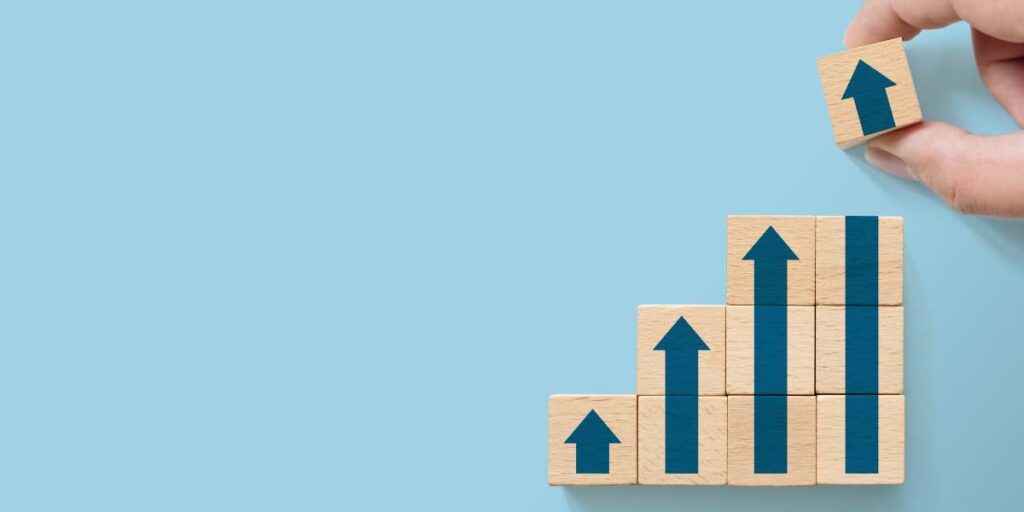
What is the minimum space required to set up an aerogel production line?
You need at least 500 square feet (46 square meters) for a small-scale setup. For industrial-scale production, plan for larger areas (typically 2,000-5,000 square feet or 185-464 square meters) to accommodate workflow and future expansion.
How much does it cost to start an aerogel production line?
Costs vary based on scale. A laboratory-scale setup starts at $10,000, while industrial-scale production can exceed $500,000. Equipment, raw materials, production capacity, and automation level significantly impact total costs. Aerogel Machinery offers scalable solutions to fit your budget.
Can I produce aerogels without supercritical drying?
Yes, alternative methods like ambient pressure drying exist. However, these methods may compromise quality. Consult experts at AerogelMachinery.com to determine the right drying method for your goals.
What are the main components of a professional aerogel production line?
A complete production line includes sol-gel preparation equipment (reactors, mixers), aging systems, solvent exchange units, drying systems (typically supercritical), post-processing equipment (cutting, shaping), and quality control instruments. Automation and control systems integrate these components for efficient operation.
What support does Aerogel Machinery provide for production line setup?
Aerogel Machinery provides end-to-end support, including equipment selection guidance, facility design consultation, on-site installation and commissioning, operator training, process optimization, R&D collaboration for product development, and ongoing technical support. Reach out to Aerogel Machinery for a consultation. Our expertise ensures your production line meets industry standards and market demands.
Leave a Reply