Our precision-engineered 29-Liter Supercritical CO2 Drying System bridges the gap between laboratory research and industrial production, providing the optimal platform for consistent, high-quality aerogel manufacturing. Purpose-built for both research facilities and small-scale industrial applications, this system delivers exceptional results through controlled supercritical CO2 drying processes.
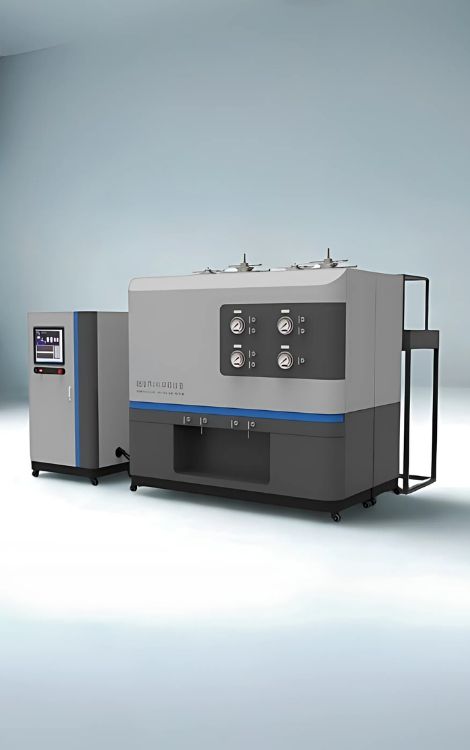
Description
Specification
Key Features & Benefits
The 29L Supercritical CO2 Drying System represents the ideal scale for optimizing aerogel production parameters before full industrial deployment. The system enables precise control over the critical phase transition that defines successful aerogel manufacturing.
During operation, the system:
- Replaces pore liquid in the wet gel with liquid CO₂ through controlled solvent exchange
- Elevates temperature and pressure above the CO₂ critical point (31.1°C, 7.38 MPa)
- Eliminates surface tension by maintaining supercritical conditions
- Preserves the delicate nanoporous structure during controlled depressurization
This carefully managed process maintains the extraordinary properties of your aerogels, including their ultra-low density, high surface area, and exceptional thermal insulation capacity.
Vessel Material | 0Cr18Ni9 (304 Stainless Steel equivalent) |
Vessel Volume | 29 Liters (Effective Working Volume) |
Inner Chamber Dimensions | Customizable to specific requirements |
Vessel Configuration | Standard single vessel (Dual vessel available) |
Maximum Working Pressure | < 22 MPa (220 bar) |
Maximum Working Temperature | < 280°C |
Opening Method | Patented quick-opening mechanism with sealing ring |
Material Basket | Standard configuration includes 1 basket (Optional liquid material basket available) |
Heating Method | Ceramic element jacket heating for precise temperature control |
Working Medium | Carbon Dioxide (CO₂) |
Control System | Automated PLC with touchscreen interface |
Safety Features | Redundant pressure relief, emergency shutdown system |
What is Supercritical CO2 Drying and Why It Matters for Aerogels?
Supercritical CO2 drying represents the critical final step in aerogel production that preserves the extraordinary properties of these remarkable materials.This process is essential because it eliminates the destructive surface tension that would otherwise collapse the delicate nanoporous structure during conventional drying methods.
During this sophisticated process:
- The wet gel containing solvent within its pores is placed in the pressure vessel
- The vessel is pressurized with CO2 and heated above the critical point (31.1°C, 73.8 bar)
- At this supercritical state, there is no distinct liquid-gas interface, eliminating surface tension
- The supercritical CO2 completely replaces the original solvent in the gel structure
- Pressure is gradually reduced while maintaining temperature, allowing CO2 to transition to gas without creating destructive surface tensions
This process preserves over 90% of the original porous volume, maintaining the unique structural integrity that gives aerogels their exceptional thermal insulation properties.
You may also want to know…
What types of aerogels can be produced with this system?
The 29L Supercritical CO2 Drying System is designed to process a wide range of aerogel formulations, including silica aerogels, organic/polymer aerogels (such as resorcinol-formaldehyde), carbon aerogels, and various composite aerogels. The temperature and pressure capabilities accommodate most common aerogel precursors requiring supercritical drying.
How does the 29L capacity compare to laboratory and industrial systems?
At 29 liters, this system represents an ideal scale-up bridge between typical laboratory equipment (1-10L) and full industrial production (1000L+). This capacity allows meaningful production quantities for product testing and specialized applications while providing directly transferable process parameters for larger-scale manufacturing.
What supporting equipment is required for operation?
The system requires standard laboratory utilities including 3-phase power (specifications provided during site assessment), cooling water for the condenser system, and a CO₂ supply (typically standard gas cylinders with siphon tube). Our technical team provides complete utility requirements during the consultation phase to ensure smooth installation and commissioning.
GET IN TOUCH