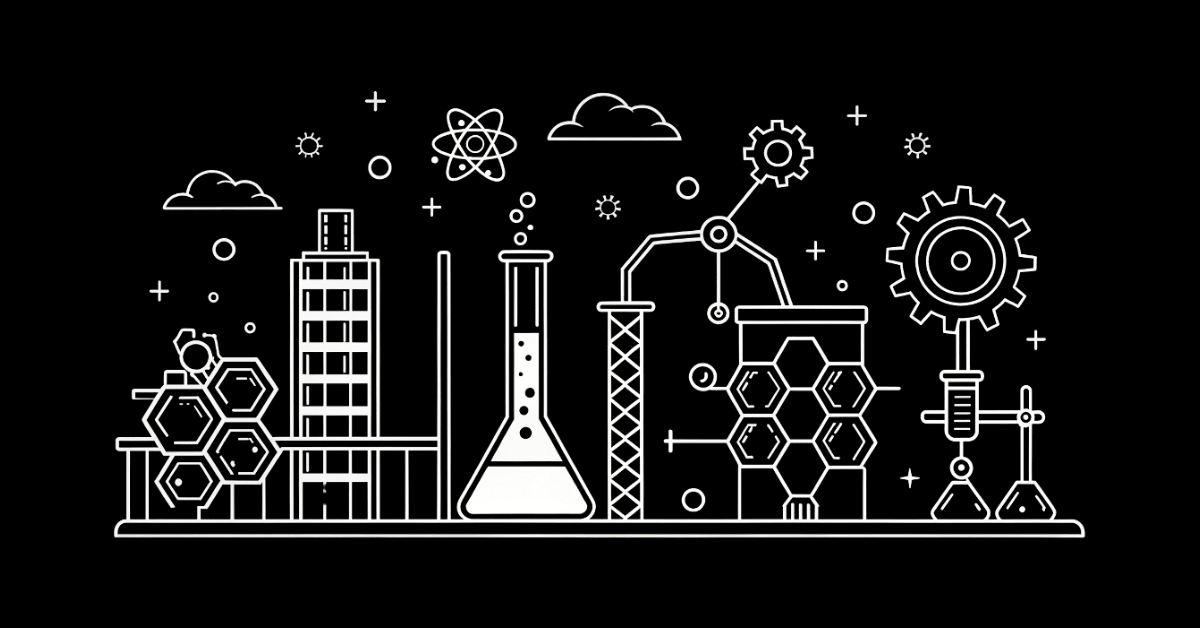
Creating a true aerogel is like performing a magic trick on the molecular level. One wrong move, and your extraordinary material becomes just another ordinary substance.
Most material scientists face a common frustration: watching promising aerogel structures collapse during drying, wasting weeks of careful preparation and valuable resources.
But what if you could consistently transform wet gels into perfect aerogels with predictable, exceptional properties?
Enter advanced aerogel drying methods—the critical techniques that separate successful aerogel production from expensive failures. In this comprehensive guide, we’ll reveal exactly how each aerogel drying technique works, when to use them, and which delivers the optimal results for your specific application.
Let’s zoom into the science behind these remarkable materials.
Key Takeaways
- Drying is the make-or-break step in aerogel manufacturing process—conventional drying destroys the nanostructure through capillary forces that can reach up to 200 MPa.
- Supercritical drying aerogel remains the gold standard for producing the highest-quality aerogels but requires specialized equipment and has the highest environmental impact.
- Freeze drying aerogel eliminates destructive capillary forces through sublimation and works well for acoustic applications due to its larger pore structure.
- Ambient pressure drying aerogel has evolved dramatically, now producing aerogels with properties nearly identical to supercritically dried materials at a much lower cost and environmental impact.
- Recent research shows properly executed ambient pressure drying can achieve thermal conductivity of 23.6 mW/m·K and porosity of 97.4%—matching supercritical drying results.
- Environmental impact varies significantly—freeze drying has the lowest global warming potential (4.41-9.90 kg CO₂eq), while supercritical drying has the highest (23.6-164.9 kg CO₂eq).
Table of Contents
The Fundamental Challenge: Why Ordinary Drying Destroys Aerogels
Before diving into specific aerogel drying methods, you need to understand why conventional drying fails so spectacularly with aerogels.
The problem isn’t the gel—it’s physics working against you.
Aerogel production begins with sol-gel chemistry, where precursors like tetraethyl orthosilicate (TEOS) or tetramethoxysilane (TMOS) undergo hydrolysis and condensation reactions. This creates a three-dimensional network of silica nanoparticles suspended in a liquid—what we call a “wet gel” or “alcogel.”
This is where conventional wisdom falls apart.
As liquid evaporates during normal drying, something destructive happens: surface tension creates capillary forces that crush the gel’s delicate nanoporous structure. These capillary pressures aren’t minor—they can reach up to 200 MPa, more than enough to collapse the nanoporous network. Journal of Sol-Gel Science and Technology, 2024
The result? A xerogel—a dense, collapsed material lacking the extraordinary properties that make aerogels valuable.
The solution isn’t trying harder with conventional methods. You need to eliminate the fundamental problem: the liquid-vapor interface that creates these destructive capillary forces.
Mastering Supercritical Drying: The Gold Standard Approach
The Science That Makes It Work
Supercritical drying aerogel represents the most established method for producing high-quality aerogels. Its power comes from a fascinating property of physics that most people never encounter: the supercritical state.
When a substance goes supercritical, it’s neither liquid nor gas—it’s both simultaneously.
This eliminates the liquid-vapor interface entirely, which means no surface tension and complete surface tension elimination. The wet gel transforms into an aerogel without the structural collapse that conventional drying causes.
Think of it as the difference between removing a support beam from a building (conventional drying) versus carefully dissolving it while maintaining all its structural properties (supercritical drying).
Low-Temperature CO₂ Supercritical Drying
The most common approach today uses supercritical CO2 drying, with carbon dioxide as the supercritical fluid, operating at relatively mild conditions of 31.1°C and 7.4 MPa.
The process follows these key steps:
- The wet gel (typically containing ethanol) is placed in a high-pressure vessel
- Liquid CO₂ gradually replaces the original solvent through multiple exchanges
- The system is heated and pressurized above CO₂’s critical point (31.1°C, 7.4 MPa)
- The supercritical CO₂ is slowly vented, leaving behind the intact aerogel structure
The results speak for themselves: silica aerogel synthesis via supercritical CO₂ drying exhibit extraordinary properties, including thermal conductivity as low as 23.6 mW/m·K, specific surface area of 473.8 m²/g, and porosity of 97.4%. RSC Advances, 2022
High-Temperature Supercritical Drying
Before CO₂ became the standard, high-temperature supercritical drying used the original alcohols (typically methanol or ethanol) as the supercritical fluid.
This approach operates at more extreme conditions (250-300°C and 8-10 MPa) and carries higher safety risks due to the flammability of alcohols under these conditions.
So why would anyone still use it? Because it eliminates the solvent exchange in aerogels – step required for CO₂ drying, potentially simplifying the process for certain applications.
The Supercritical Reality Check
Despite producing the highest-quality aerogels, supercritical drying comes with significant drawbacks:
- High energy consumption: Maintaining supercritical conditions requires substantial energy input
- Specialized equipment: A professional euipment supplier (like us!) is required for making the high-pressure vessels and control systems
- Safety concerns: Working with high pressures and temperatures inherently carries risks
- Environmental impact: Even with 95% CO₂ recycling, this method accounts for approximately 28% of the global warming potential in aerogel production Journal of Sol-Gel Science and Technology, 2024
These factors have driven the search for alternative aerogel drying techniques that might deliver comparable results without the drawbacks.
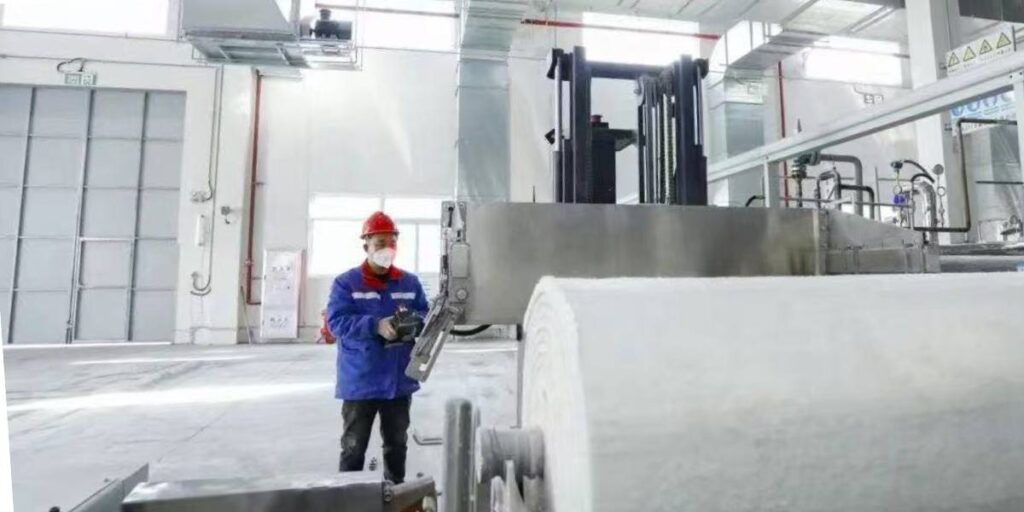
Leveraging Freeze Drying Aerogel: The Sublimation Advantage
Freeze drying takes a completely different approach to eliminating the destructive liquid-gas interface. Instead of pushing beyond it through supercritical conditions, freeze drying sidesteps the problem entirely by avoiding the liquid phase.
The Science Behind the Method
The fundamental concept behind freeze drying aerogel production methods is sublimation—the direct transition of a substance from solid to gas without passing through the liquid phase.
By freezing the liquid in the gel and then removing it as a vapor, freeze drying eliminates the surface tension that destroys the gel’s structure during conventional drying.
This process creates materials sometimes called “cryogels,” which, while technically different from aerogels in some respects, can achieve remarkable properties in their own right.
The Freeze-Drying Process Breakdown
The freeze drying process follows three key steps:
- Freezing: The wet gel is frozen at very low temperatures (-20°C to -80°C), converting the liquid in the pores to solid ice
- Primary Drying: Under vacuum conditions (0.014-0.018 mBar), the ice sublimates directly to vapor
- Secondary Drying: Optional heating removes any remaining moisture RSC Advances, 2022
This approach requires specialized equipment including freeze dryers capable of maintaining deep vacuum conditions.
Results That Might Surprise You
Recent research demonstrates that freeze-dried aerogels can achieve impressive properties:
- Thermal conductivity of 23 mW/m·K
- Specific surface area of 369.4 m²/g
- Porosity of 96.7%
While the specific surface area is somewhat lower than supercritically dried aerogels, the thermal performance is remarkably similar—making this approach viable for many applications.
The Freeze-Drying Trade-Offs
Like any method, freeze drying comes with its own advantages and challenges:
Advantages:
- Eliminates the need for high-pressure equipment
- Preserves original surface chemistry without modification
- Can use water as the primary solvent (environmentally friendlier)
- Well-suited for temperature-sensitive materials
Disadvantages:
- Ice crystal formation can disrupt the original gel network
- Energy-intensive freezing and vacuum requirements
- Significantly longer processing times compared to other methods
- Typically produces materials with larger pores than supercritical drying
Ambient Pressure Drying: Making Aerogels Accessible
Most revolutionary technologies follow a predictable path: they begin as complex, expensive processes available only to specialists, then gradually become simpler and more accessible.
Ambient pressure drying represents this democratization of aerogel technology.
Operating at normal atmospheric pressure and moderate temperatures, this approach has transformed aerogels from exotic laboratory curiosities into practical materials for widespread application.
Surface Modification: The Chemical Solution
The key innovation that makes ambient pressure drying possible is surface modification of the gel before drying.
By chemically altering the gel surface to make it hydrophobic (water-repelling), these hydrophobic treatments dramatically reduce the capillary forces that would otherwise collapse the structure during drying.
The process relies on silylating agents like trimethylchlorosilane (TMCS) or hexamethyldisilazane (HMDS) that replace hydroxyl groups on the silica surface with hydrophobic groups.
This creates what scientists call the “spring-back effect”—after initial shrinkage during drying, the modified network actually expands back to near its original volume.
Step-by-Step Approach to Ambient Pressure Drying
The typical ambient pressure drying process involves:
- Solvent exchange to replace water with a lower surface tension solvent (typically ethanol)
- Surface modification using silylating agents
- Controlled evaporation at ambient pressure and moderate temperatures (typically 40-80°C)
Recent innovations have streamlined this process further, with one-pot approaches that integrate gelation and surface modification in a single step.
The Ambient Pressure Revolution: Results and Trade-offs
Recent research (RSC Advances, 2022) has delivered a surprising conclusion: properly executed ambient pressure drying can produce aerogels with properties remarkably similar to supercritically dried materials.
Studies show these aerogels achieving:
- Thermal conductivity of 23.6 mW/m·K
- Specific surface area of 473.8 m²/g
- Porosity of 97.4%
These results challenge the conventional wisdom that supercritical drying is always superior.
Despite being the advocate and leading solution provider for aerogel’s ambient pressure method, at Aerogel Machinery, we have to be fully open and transprarent about the trade-offs. This, however, include:
- Higher solvent requirements
- Highest dependency on the techniques and commercial-production experiences
- Modified surface chemistry that may affect certain applications
- Some shrinkage (typically 30-50% linear) compared to supercritical drying
- Limited applicability to certain gel compositions
Comparison of Aerogel Drying Methods: A Data-Driven Approach
Choosing the optimal aerogel drying method requires balancing multiple factors: desired material properties, available equipment, budget constraints, and environmental considerations.
Property Comparison: Numbers Don’t Lie
Let’s compare the key properties of aerogels produced by different drying methods:
Property | Supercritical Drying | Freeze Drying | Ambient Pressure Drying |
---|---|---|---|
Thermal Conductivity (mW/m·K) | 23.6 | 23.0 | 23.6 |
Specific Surface Area (m²/g) | 473.8 | 369.4 | 473.8 |
Porosity (%) | 97.4 | 96.7 | 97.4 |
Average Pore Width (nm) | ~10 | ~16 | ~10 |
Bulk Density (g/cm³) | ~0.06 | ~0.10 | ~0.06 |
The surprising conclusion? When executed properly, ambient pressure drying can produce aerogels with properties nearly identical to supercritically dried materials.
Environmental Impact: The Hidden Factor
The environmental footprint of aerogel production is increasingly important. Life cycle assessment studies reveal significant differences between methods:
Drying Method | Global Warming Potential (kg CO₂eq) | Energy Consumption | Solvent Requirements |
---|---|---|---|
Supercritical CO₂ | 23.6-164.9 | High | Moderate-High |
Ambient Pressure | 6.30-28.8 | Moderate | High |
Freeze Drying | 4.41-9.90 | High (electricity) | Low |
These numbers tell a clear story: freeze drying and ambient pressure drying generally have lower environmental impacts than supercritical drying, primarily due to reduced energy requirements and/or higher solvent recycling potential.
Application-Specific Selection Guide
Different applications prioritize different properties:
- Thermal insulation: Supercritical drying or ambient pressure drying (lowest thermal conductivity)
- Acoustic insulation: Freeze drying (larger pore structure beneficial for sound absorption)
- Catalyst supports: Supercritical drying (highest surface area and controlled pore structure)
- Drug delivery: Supercritical drying or freeze drying (better control of release kinetics)
- Oil spill remediation: Ambient pressure drying with hydrophobization (high oil absorption capacity)

The key is matching the method to your specific requirements, rather than assuming one approach is universally superior.
The Future of Aerogel Production: Emerging Innovations
The landscape of aerogel drying methods continues to evolve rapidly, with several exciting developments on the horizon.
Hybrid Approaches: Getting the Best of Both Worlds
At Aerogel Machinery, we have being working with academic partners and research groups all over the industry, and we are currently exploring hybrid drying approaches that combine elements of different methods to optimize both material properties and environmental impact.
For example, partial freeze drying followed by ambient pressure drying may reduce energy consumption while maintaining key material properties.
Process Intensification: Faster, Better, More Efficient
Integration of multiple processing steps and optimization of process parameters can significantly reduce energy consumption and processing time.
Recent advances in rapid supercritical extraction demonstrate the potential for more efficient processing, reducing environmental impact by up to 30% compared to traditional supercritical drying. (Karatum, O., Bhuiya, M.M.H., Carroll, M.K., Anderson, A.M. and Plata, D.L. (2018), Life Cycle Assessment of Aerogel Manufacture on Small and Large Scales: Weighing the Use of Advanced Materials in Oil Spill Remediation. Journal of Industrial Ecology, 22: 1365-1377. doi.org)
Sustainability: As Always
The environmental footprint of aerogel production is getting increasing attention, with several strategies emerging to enhance sustainability:
- Raw Material Selection: Water glass (sodium silicate) derived from renewable energy sources shows 20-29% lower CO₂ emissions compared to traditional TEOS-based routes Cement and Concrete Research, 2017
- Biobased Precursors: Materials such as cellulose, starch, and alginate can reduce global warming potential by 60-100% compared to conventional silica-based routes Journal of Building Engineering, 2021
- End-of-Life Considerations: Some biobased aerogels offer biodegradability advantages, with certain lignin-gelatin aerogels completely biodegrading within 14 days Cell Reports Physical Science, 2024
These innovations are not just environmentally responsible—they’re economically essential as sustainability becomes an increasingly important factor in material selection across industries.
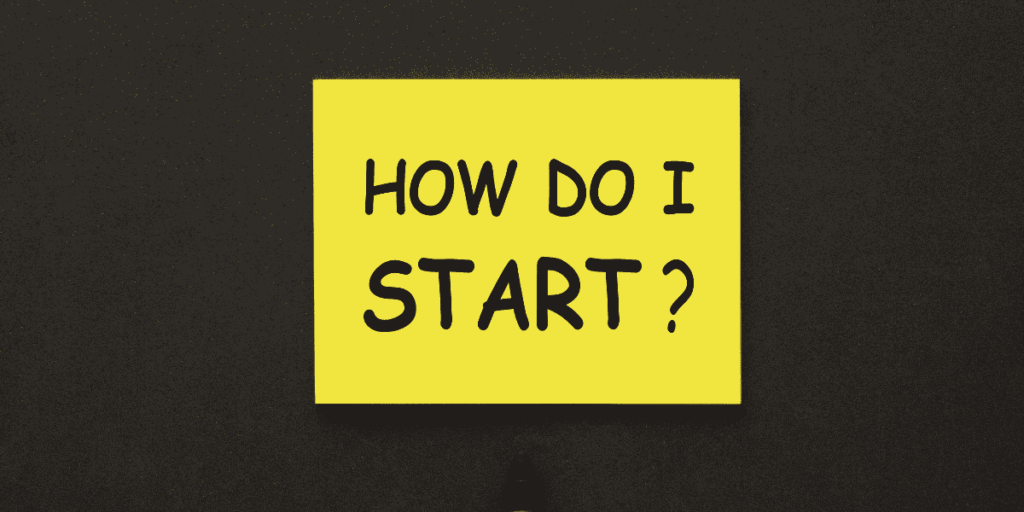
How to Choose the Best Aerogel Drying Method: Your Decision Framework
Here’s the truth most experts won’t tell you: there is no “best” drying method for aerogels—only the method that best matches your specific requirements.
Use this decision framework to guide your selection:
- Property requirements: If you need the absolute lowest density and thermal conductivity, prioritize supercritical or optimized ambient pressure drying
- Equipment availability: Your access to top-quality high-pressure equipment may necessitate ambient pressure or freeze drying approaches (not a case here since you’ve found us!)
- Budget constraints: Consider both capital investment (highest for supercritical drying) and operational costs (energy, solvents, maintenance)
- Production volume: Larger volumes may favor ambient pressure drying for practical reasons
- Environmental priorities: If minimizing carbon footprint is essential, lean toward freeze drying or optimized ambient pressure approaches
- Material compatibility: Consider whether your specific formulation is compatible with surface modification (required for ambient pressure drying)
Conclusion
The selection of appropriate aerogel drying methods represents the critical factor in successful aerogel production, directly influencing material properties, manufacturing costs, and production scalability. Through our comprehensive equipment and technology solutions at Aerogel Machinery LLC, we’ve witnessed firsthand how the right drying technology transforms challenging production processes into reliable manufacturing systems.
While supercritical drying delivers exceptional material properties, ambient pressure and freeze drying offer compelling alternatives for specific applications—each with distinct advantages that align with different production requirements. As the practical pioneer in aerogel production equipment, Aerogel Machinery provides specialized systems covering all major aerogel drying methods, enabling both researchers and manufacturers to select optimal approaches for their specific needs.
Our systematic ANALYZE-ENGINEER-IMPLEMENT-OPTIMIZE methodology ensures that clients receive not just equipment, but complete manufacturing solutions tailored to their specific aerogel formulations and production goals. By engineering drying systems with precision control and reliability, we make advanced aerogel drying methods accessible to organizations ranging from research laboratories to industrial manufacturers.
The extraordinary potential of aerogels across industries—from construction and aerospace to energy storage and environmental remediation—demands production equipment that delivers consistent quality without the failures common in conventional approaches. Aerogel Machinery LLC’s integrated production systems, featuring state-of-the-art drying equipment and comprehensive process control, enable organizations to harness these remarkable materials with confidence.
Whether you’re exploring laboratory-scale aerogel production or scaling to industrial manufacturing, selecting the right drying technology partner is the foundation of manufacturing success. Contact our team to discover how our specialized equipment can transform your aerogel production capabilities.
Can aerogel drying methods be combined to optimize both cost and quality?
Yes, hybrid drying approaches represent a promising frontier in aerogel research. For example, combining partial freeze drying with ambient pressure techniques can reduce energy consumption while preserving key material properties. Recent research shows that sequential approaches can achieve thermal conductivities as low as 24 mW/m·K while reducing production costs by 15-30% compared to traditional supercritical drying alone. Some manufacturers are already implementing “modified supercritical extraction” that integrates elements from multiple techniques, creating processing routes that balance quality, cost, and environmental impact.
Our team at Aerogel Machinery is here to help you identifying which properties are essential for your specific application and optimizing the combined approach accordingly.
How long does each aerogel drying method typically take from start to finish?
Drying times vary significantly between methods, impacting both production schedules and energy costs:
– Supercritical CO₂ drying: 8-24 hours (including solvent exchange)
– High-temperature supercritical drying: 4-12 hours (faster but higher energy)
– Ambient pressure drying: 24-72 hours (varies with sample thickness)
– Freeze drying: 48-96+ hours (longest process)
Recent process optimizations have reduced supercritical drying times by up to 40% through modified temperature-pressure ramping protocols. Ask us how!
What’s the real-world cost difference between these aerogel drying methods?
The cost differences between drying methods are substantial. Supercritical CO₂ drying requires expensive high-pressure equipment and uses the most energy, making it several times more costly than alternatives. Ambient pressure drying is the most economical option, with lower equipment needs and moderate energy use, despite higher solvent requirements. Freeze drying falls in the middle range for both equipment and operating costs.
With the help from Aerogel Machinery LLC, especially at industrial scale, all methods become much more cost-effective, with ambient pressure drying offering the best economics for mass production.
Leave a Reply