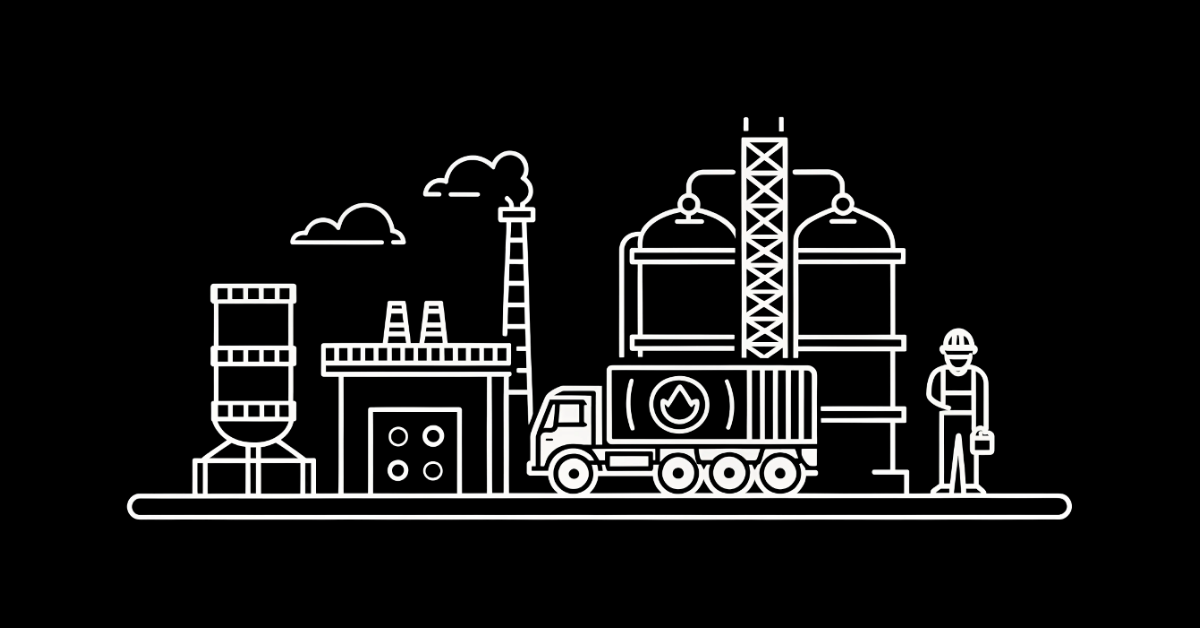
Ever stared at a quote for aerogel manufacturing equipment and wondered if you’re about to make a million-dollar mistake?
You’re not alone. The ultra-specialized world of aerogel production equipment leaves even experienced engineers scratching their heads about what’s actually necessary versus what’s just expensive.
The truth? Your aerogel equipment selection strategy is the foundation that either amplifies or cripples everything else in your aerogel production process. Get it right, and you’re positioned for efficient, profitable manufacturing. Get it wrong, and you’re facing endless technical problems, inconsistent quality, and budget overruns that could have been avoided.
This isn’t just another technical guide. It’s your roadmap to transforming a complex silica aerogel manufacturing process into a strategic advantage.
Whether you’re setting up a research laboratory or scaling to industrial production, we’ll show you exactly what aerogel equipment you need, how to evaluate it properly, and how to make decisions that align with your specific manufacturing goals.
Stop gambling with your aerogel production line setup nvestment. It’s time to approach this process like the experts do.
Key Takeaways
- Specialized Aerogel Equipment Requirements: Aerogel manufacturing machinery demands purpose-built equipment for each production phase: sol-gel preparation, aging, and the critical drying process
- Scale Determines Approach: Laboratory equipment (1-2,000mL capacity) prioritizes precision while industrial aerogel production systems (50-3,000L) focus on reliability and throughput
- Drying Technology Is Critical: Supercritical drying equipment for aerogels represents your most crucial investment decision, directly impacting final aerogel quality and properties
- Budget Reality: Entry-level research systems start around $10,000, while complete aerogel production plant systems require significant capital investment with emphasis on operational efficiency
- Vendor Expertise Matters: Selecting suppliers with aerogel-specific experience dramatically increases your implementation success rate
Table of Contents
Understanding Essential Aerogel Manufacturing Equipment
Most manufacturing failures begin with misunderstanding what aerogel equipment is actually needed.
Aerogel production isn’t just another manufacturing process—it’s a sophisticated choreography of chemical reactions, aging, and precision drying. The equipment supporting this process must be equally sophisticated.
The foundation of any aerogel production system lies in supporting the fundamental chemistry. The sol-gel process involves two critical chemical reactions: hydrolysis, where silica precursors like TEOS react with water to form silanol groups, and condensation, where these silanol groups form siloxane bonds, creating the three-dimensional network that characterizes aerogels.
Your aerogel equipment selection varies dramatically between laboratory and industrial settings. Laboratory equipment prioritizes precision and experimental flexibility, while industrial-scale aerogel production systems focus on reliability, throughput, and cost efficiency. This fundamental difference impacts everything from vessel design to control systems.
Have you considered how your specific application requirements determine your equipment configuration? The properties you need in your final aerogel product—whether thermal insulation materials, catalytic properties, or specialized applications—will influence your equipment selection from day one.
Core Equipment Components for Any Aerogel Production Setup
Here’s the truth most aerogel equipment vendors won’t tell you: regardless of scale, certain core components are non-negotiable for successful aerogel manufacturing.
- Sol-gel processing equipment: These include mixing vessels with precise temperature control and stirring capabilities. For laboratory settings, this typically involves beakers, round-bottom flasks, and magnetic stirrers. Larger industrial systems require more sophisticated reactor vessels with advanced mixing systems.
- Aging vessels with temperature control: After initial gel formation, aging vessels allow for strengthening of the silica network. This equipment must provide stable temperature conditions and appropriate containment for the duration of the aging process, which significantly improves the mechanical properties of the final aerogel.
- Drying equipment: The most critical component of any aerogel production system. Supercritical drying equipment includes high-pressure vessels capable of reaching the critical point of the solvent (typically CO2), along with precise pressure and temperature control systems. Alternative drying methods require their own specialized equipment.
- Process control and monitoring systems: These include temperature, pressure, and flow sensors, along with analytical instruments for quality control. Laboratory systems might include FTIR, BET, XRD, and SEM equipment for detailed characterization.
Most manufacturers make the mistake of underestimating the importance of monitoring systems. Don’t be one of them. Your process control technology often determines whether you’re producing premium aerogels or inconsistent, subpar materials.

The Critical Role of Drying Equipment in Aerogel Production
Let me be direct: your drying equipment selection will make or break your entire aerogel operation.
Supercritical drying is fundamentally necessary for producing true aerogels. This process is critical because it prevents the collapse of the porous network by eliminating surface tension and capillary forces that would otherwise destroy the delicate aerogel structure. At the supercritical state, there is no distinct liquid-gas interface, allowing the solvent to be removed while preserving up to 99% of the original porous volume.
There are two primary approaches to supercritical drying:
- Low-temperature supercritical drying (the Hunt Process): In this method, the organic solvent in the gel (typically ethanol or acetone) is first replaced with liquid carbon dioxide by soaking. Carbon dioxide reaches its supercritical point at much lower temperature (31.1°C) and reasonable pressure (72.8 atm), making it safer and more energy-efficient than high-temperature methods. This approach typically results in about 5% shrinkage of the final aerogel. Aerogel.org
- High-temperature supercritical drying: This method directly brings the solvent within the gel (typically methanol) to its critical point, which requires temperatures of 300-600°C and pressures of 50-100 atm. While more hazardous due to the flammability of organic solvents at these conditions, this method can produce higher-quality aerogels with minimal shrinkage. For silica aerogels, methanol at its critical point can react with surface hydroxyl groups to form methoxy groups, creating partially hydrophobic aerogels.
Alternative drying methods produce different results with their own equipment requirements:
- Ambient pressure drying (APD): This process involves surface modification of the gel with alkyl groups to eliminate terminal silanols before evaporative drying. Equipment for APD typically includes specialized chemical reactors for silylation (using agents like trimethylchlorosilane or hexamethyldisilazane) and conventional ovens for the final drying step. APD typically yields nanoporous materials with up to 95% porosity but with some limitations in size and shape. NCBI
- Freeze drying: This method involves freezing the gel and then removing the solvent by sublimation under vacuum. Equipment includes freezers capable of reaching -50 to -85°C and vacuum systems with effective cold traps (-80°C to -100°C). Freeze-dried aerogels (sometimes called “cryogels”) typically have different structures than supercritically dried aerogels, often with lower surface areas and different pore volumes. ScienceDirect
Your drying equipment selection directly impacts final product quality. The precision of temperature and pressure control during the drying phase dramatically affects the structural integrity, porosity, and performance characteristics of the finished aerogel. This makes drying equipment the single most consequential investment decision in your aerogel production line.
Laboratory-Scale Equipment: What You Actually Need
Most researchers waste thousands on aerogel equipment features they’ll never use while missing critical components that determine experiment success.
Laboratory-scale aerogel production systems serve as both research platforms and proving grounds for scaling to industrial production. Your equipment choices at this stage set the foundation for everything that follows.
Laboratory equipment prioritizes precision over volume. These systems typically handle small batches while providing maximum control over process variables, allowing researchers to experiment with formulations and conditions to optimize aerogel properties.
Typical laboratory supercritical drying systems process relatively small volumes. Standard capacities range from as little as 60mL up to 2,000mL, depending on the specific research needs and available budget. Laboratory-scale critical point dryers are available commercially, with prices typically ranging from $10,000 to $30,000 for new equipment.
DIY approaches can significantly reduce costs, with custom-built “manuclaves” costing between $550−1,500 for basic laboratory systems without windows or specialized features. These DIY systems can be assembled from high-pressure components available from suppliers like McMaster-Carr, though they require careful attention to safety considerations.
Ask yourself: What specific research objectives are driving your equipment selection? Whether you’re developing novel aerogel formulations, optimizing existing processes, or preparing for industrial scaling, your equipment needs will differ significantly.
Essential Equipment for Laboratory Aerogel Research
A comprehensive laboratory setup typically includes:
- High-pressure autoclaves for supercritical drying: Small-scale autoclaves or high-pressure vessels specifically designed for supercritical fluid extraction. These systems must safely reach and maintain the critical pressure and temperature of the drying medium (typically CO2).
- Temperature and pressure control systems: Precision controllers that maintain exact conditions during the critical drying process. This includes heating mantles, cooling systems, pressure regulators, and monitoring equipment.
- Safety systems: Given the high pressures involved in supercritical drying, appropriate safety systems including pressure relief valves, rupture disks, and monitoring equipment are essential. Safety considerations include proper vessel design with appropriate pressure ratings (typically 1,500-3,000 psi for CO2 systems) and quality materials (316 stainless steel is commonly used). Aerogel.org
- Analytical equipment: Instruments for characterizing aerogel particles and properties, including vacuum pumps, filtration systems, and analytical instruments such as FTIR, BET, XRD, and SEM for monitoring gel structure and porosity.
For freeze drying systems at laboratory scale, essential components include:
- Freezing equipment capable of reaching -50 to -85°C
- Vacuum systems capable of achieving pressures below 0.002 mbar
- Cold traps capable of -80 to -100°C for capturing sublimed water/solvents
- Temperature-controlled shelves for controlled processing ScienceDirect
Most labs overlook the importance of proper analytical equipment. Without it, you’re essentially manufacturing blind—unable to verify the quality of what you’re producing.
Budget Considerations for Laboratory Setups
Let’s be real about the financial investment required:
- Initial investment vs. capabilities: Entry-level research systems provide basic functionality while more sophisticated systems offer greater precision, automation, and analytical capabilities. For supercritical drying systems, manual operation typically costs significantly less than automated systems.
- Ongoing operational costs: Beyond the initial investment, factor in the costs of consumables (CO2, solvents, precursors) and maintenance requirements. For supercritical CO2 systems, the primary operational expense is the CO2 itself, which costs approximately $2-5 per liter of liquid CO2 depending on your location and supplier.
- Equipment versatility: Consider whether the equipment can be adapted for various aerogel formulations or is limited to specific chemistries. Equipment that offers flexibility may provide better long-term value.
- Scaling potential: If industrial production is your eventual goal, select laboratory equipment that facilitates process optimization and transfer to larger scales.
For ambient pressure drying, lab-scale costs are generally lower since specialized high-pressure equipment isn’t required. However, the chemical costs may be higher due to the specialty silylating agents needed. Silylating agents like trimethylchlorosilane (TMCS) and hexamethyldisilazane (HMDS) can cost between $50-200 per liter depending on purity and quantity. NCBI
The mistake most researchers make? Focusing exclusively on the initial equipment price while ignoring operational costs that accumulate over time. A slightly higher initial investment in quality equipment often delivers substantial savings over the equipment’s lifetime.
Industrial-Scale Aerogel Production Systems
Scaling up isn’t just about bigger equipment. It’s an entirely different manufacturing paradigm.
Transitioning from laboratory to industrial aerogel production introduces new equipment considerations centered around efficiency, consistency, and cost-effectiveness. What works in the lab often fails spectacularly at scale without proper adaptation.
Industrial equipment prioritizes reliability and throughput. While laboratory equipment focuses on flexibility and precision for small batches, industrial systems must deliver consistent quality at scale, often with greater automation to reduce labor costs and variability.
Industrial systems for supercritical drying typically feature multiple high-pressure vessels operating in parallel or in sequence to enable continuous or semi-continuous processing. Industrial-scale supercritical drying equipment capacities typically range from 50 to 3,000 liters, with larger systems consisting of multiple vessels operating in parallel.
Investment decisions must balance capital and operational costs. Industrial equipment represents a significant capital investment, but proper selection can dramatically reduce per-unit production costs through improved efficiency, reduced waste, and increased throughput.
Key Components of Industrial Aerogel Production Lines
Industrial aerogel production systems typically include:
- Larger reactors with sophisticated mixing systems: Industrial-scale vessels equipped with advanced mixing technologies to ensure uniform reaction conditions throughout larger volumes.
- Automated process control systems: Comprehensive monitoring and control systems that maintain precise conditions throughout the production process, ensuring consistent quality across batches. These systems typically include distributed control systems (DCS) or programmable logic controllers (PLC) with human-machine interfaces.
- Solvent recovery systems: Given the larger volumes involved in industrial production, solvent recovery becomes economically significant. These systems capture and purify solvents for reuse, reducing operational costs and environmental impact. For supercritical CO2 systems, the CO2 can be recycled by condensing it after depressurization, significantly reducing operational costs. Thyssenkrupp Uhde
- Safety and monitoring systems: Comprehensive safety features for managing the risks associated with high-pressure operations, chemical handling, and large-scale production processes. These include redundant pressure relief systems, emergency shutdown systems, and hazardous area classifications for electrical equipment.
- Integration capabilities: Systems designed to seamlessly connect with existing manufacturing infrastructure, material handling equipment, and facility utilities.
For industrial ambient pressure drying systems, corrosion-resistant materials become especially important due to the acidic byproducts of silylation reactions. Using an equimolar mixture of silylating agents like TMCS and HMDS can reduce corrosion issues by neutralizing acidic byproducts (HCl from TMCS reacts with NH3 from HMDS to form NH4Cl). NCBI
The biggest mistake industrial manufacturers make? Underestimating the importance of automated process control. At industrial scale, even minor process variations can result in millions in wasted product.
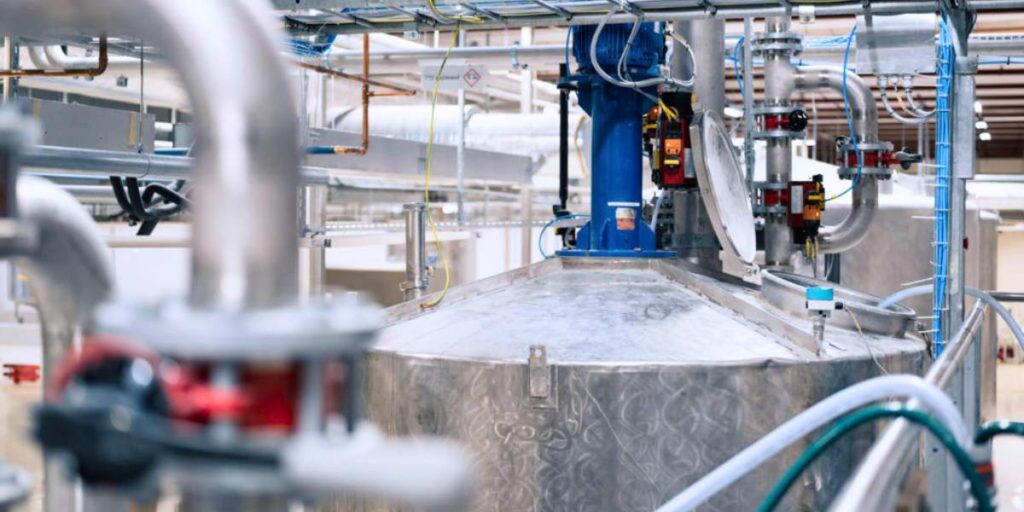
Scaling Considerations When Purchasing Equipment
Successfully scaling from laboratory to industrial production requires careful equipment selection:
- Process parameter consistency: Equipment must facilitate consistent process parameters (temperatures, pressures, mixing conditions) across different scales to ensure comparable aerogel properties.
- Material handling adaptations: As production volumes increase, material handling becomes increasingly important. Systems must efficiently move materials between process stages without compromising quality.
- Control system precision: Even at larger scales, control systems must maintain the precision necessary for aerogel production, particularly during critical phases like supercritical drying.
- Scale-appropriate safety systems: Safety requirements change with scale, requiring appropriate engineering controls for larger volumes of chemicals and higher energy systems.
- Energy efficiency: Large-scale systems should incorporate heat recovery and energy optimization to reduce operational costs. For supercritical CO2 systems, heat exchangers that recover energy during depressurization can significantly reduce energy consumption. Thyssenkrupp Uhde
Ask yourself: Is your equipment supplier experienced with successful scale-up? Most industrial aerogel production failures stem from scaling issues that could have been anticipated with proper expertise.
How to Select the Right Aerogel Equipment Vendor
Your equipment is only as good as the company that designed it.
The right aerogel manufacturing equipment vendor can be the difference between a successful aerogel production operation and a costly disappointment. This decision deserves far more scrutiny than most manufacturers give it.
Technical expertise matters more than general equipment capability. Given the specialized nature of aerogel production, vendors with specific experience in this field offer significant advantages over general equipment manufacturers.
Specialized manufacturers provide more tailored solutions. Vendors with specific aerogel production experience understand the unique challenges and requirements of these processes, resulting in more appropriate equipment design and supportive services.
Look for demonstrated process knowledge. Beyond equipment specifications, vendors should demonstrate understanding of the underlying chemical processes and how their equipment supports successful aerogel production.

Key Questions to Ask Equipment Suppliers
When evaluating potential vendors, consider asking:
- What specific aerogel formulations has your equipment successfully produced? The answer reveals their familiarity with your specific application.
- What level of process documentation and knowledge transfer is included? Comprehensive documentation and training are essential for successful implementation.
- How does your equipment address common production challenges? Their answer indicates their understanding of aerogel-specific production issues.
- What ongoing technical support is available after installation? Post-installation support can be crucial for optimizing and troubleshooting processes.
- What energy efficiency features are incorporated into the design? Energy consumption significantly impacts operational costs, particularly for larger systems.
- What is your approach to safety systems for aerogel production? Look for vendors who prioritize safety through system design, documentation, and training.
- Can you provide references from other customers producing similar materials? Direct feedback from existing customers can provide valuable insights into the vendor’s capabilities and reliability.
The common mistake most buyers make? Not asking for specific examples of successful implementations similar to their intended application. Past success is the best predictor of future performance.
The Value of Turnkey Solutions vs. Individual Components
Consider whether a turnkey aerogel production solution or individual components better suit your needs:
- Turnkey systems offer process consistency and vendor accountability. When all components come from a single vendor, integration issues are minimized, and responsibility for system performance is clear.
- Individual components may offer cost advantages but require integration expertise. Sourcing components separately may reduce capital costs but requires significant internal expertise to integrate effectively.
- Consider total cost of ownership. Beyond the initial purchase price, factor in installation, training, operational efficiency, and ongoing support when comparing options.
For supercritical drying systems, specialized vendors that understand the unique requirements of aerogel production are particularly valuable, as standard supercritical fluid extraction equipment may not be optimized for the specific needs of aerogel production, which often requires larger vessels and specialized process control.
The truth most vendors won’t tell you? Integration costs for separately sourced components often exceed any initial savings. Factor this reality into your decision-making process.
Equipment for Specific Aerogel Applications
Not all aerogel applications require the same equipment. Your specific end product dramatically changes what you need.
Different aerogel applications require specific equipment considerations that directly impact your manufacturing success. Understanding these requirements early prevents costly modifications later.
- Thermal insulation applications: Equipment must be optimized to produce aerogels with the lowest possible thermal conductivity, typically requiring precise control of pore structure and density. The thermal conductivity of high-quality silica aerogels can reach as low as 0.012 W/(m·K), significantly outperforming conventional insulation materials like fiberglass (0.042-0.046 W/(m·K)) or mineral wool (0.040-0.049 W/(m·K)). NCBI
- Hydrophobic aerogel production: Additional processing equipment may be needed for surface modification to achieve water-repellent properties. For supercritically dried silica aerogels, high-temperature methanol processing can naturally create some hydrophobicity, while ambient-pressure dried aerogels require dedicated silylation equipment to achieve water contact angles of 140-150°. NCBI
- Specialty formulations and composites: Equipment for producing aerogel composites (e.g. aerogel blankets) or specialty formulations may require additional mixing capabilities, alternative precursor handling, or modified drying parameters. For example, polymer aerogels typically require low-temperature supercritical drying as they decompose at the temperatures required for high-temperature supercritical drying. Aerogel.org
- Optical applications: For transparent aerogels, equipment must provide extremely precise control of the entire process, particularly during the critical drying phase, to maintain optical clarity. Even minor variations in pressure or temperature during supercritical drying can create stress patterns that reduce transparency.
Ask yourself: Is your equipment optimized for your specific application? Generic equipment often delivers mediocre results across all applications rather than excellence in your specific area.
Investment Planning for Aerogel Production Facilities
The equipment is just one piece of a complex production ecosystem.
Establishing an aerogel production facility involves considerations beyond equipment selection that directly impact your operational success. Ignoring these factors leads to implementation delays and budget overruns.
- Facility requirements: Consider space requirements, utility needs (electricity, water, gas), and safety systems necessary to support your production equipment. For supercritical drying operations, explosion-proof electrical classifications and proper ventilation are particularly important safety considerations.
- Operational costs: Factor in ongoing expenses including energy consumption, raw materials, maintenance, and labor. For supercritical CO2 drying systems, energy costs for compression and heating/cooling can be significant, while for ambient pressure drying, the cost of specialty silylating agents becomes a major consideration.
- Return on investment: Evaluate production capacity against market demand to ensure your investment will generate appropriate returns.
The reality most manufacturers ignore? Facility modifications often cost as much as the equipment itself. Factor these expenses into your initial budget to avoid unpleasant surprises.
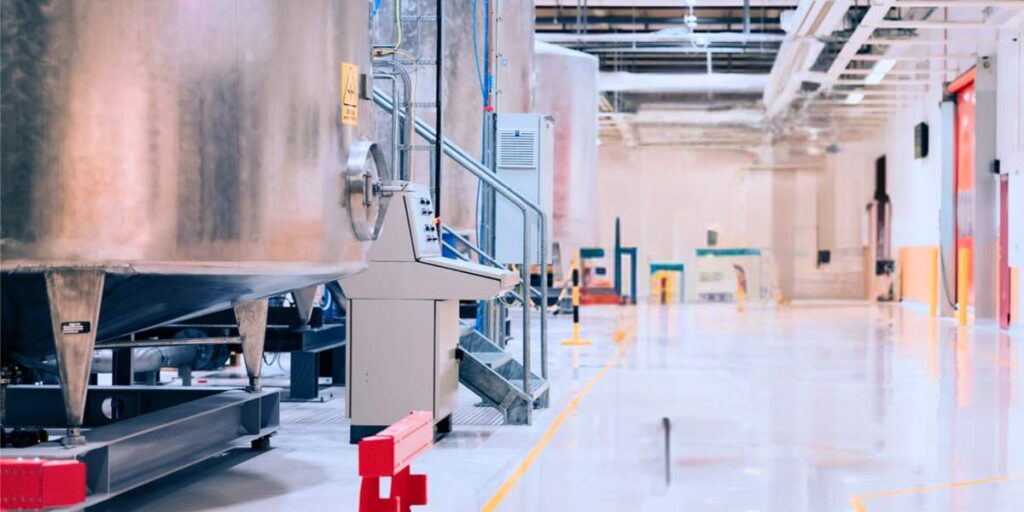
Balancing Equipment Costs Against Production Economics
When planning your investment:
- Consider long-term operational efficiency. Higher initial investment in more sophisticated equipment often leads to lower long-term operational costs through improved efficiency, reduced waste, and lower energy consumption.
- Evaluate energy recovery options. Systems with energy recovery capabilities can significantly reduce operational costs, particularly for energy-intensive processes like supercritical drying.
- Right-size your equipment. Properly sized equipment prevents resource wastage and optimizes production efficiency. Equipment that’s too large wastes resources, while undersized equipment limits production capacity.
- Compare different drying technologies. While supercritical drying produces the highest-quality aerogels, ambient pressure drying can be more economical for some applications where the highest performance isn’t required. A cost analysis should include both capital and operational expenses over the expected equipment lifetime. NCBI
The mistake most operations make? Focusing exclusively on initial equipment cost while ignoring the operational expenses that accumulate over time. Energy efficiency features often pay for themselves within 1-2 years of operation.
Ensuring Equipment Reliability and Production Consistency
Reliability and consistency are essential for profitable production:
- Implement comprehensive quality control systems. Equipment should include appropriate monitoring and control systems to ensure consistent aerogel properties across production runs.
- Develop maintenance protocols. Regular maintenance is essential for equipment reliability and longevity. Consider maintenance requirements and accessibility when selecting equipment.
- Consider redundancy for critical components. For continuous production operations, redundant systems for critical components may be necessary to prevent costly downtime.
- Plan for operational flexibility. Equipment that can accommodate multiple formulations or process conditions provides valuable flexibility as your product range evolves.
Most manufacturers underestimate the cost of downtime. A single day of production stoppage can cost tens of thousands in lost production—making reliability features worth far more than their initial cost.
Conclusion
Selecting the right aerogel production equipment represents a critical decision that impacts everything from product quality to operational efficiency and profitability. By understanding the essential components of aerogel production systems and carefully evaluating both laboratory and industrial-scale options, you can make informed investments that align with your specific application needs and business objectives.
The drying method you select—whether supercritical drying, ambient pressure drying, or freeze drying—will have profound implications for your equipment requirements, operational costs, and final product properties. Supercritical drying remains the gold standard for producing high-quality aerogels with minimal shrinkage, while ambient pressure drying offers a lower-cost alternative for applications that can tolerate some compromise in porosity or size limitations.
The difference between success and failure in aerogel manufacturing often comes down to equipment selection. Those who treat this as a strategic decision rather than a mere procurement exercise position themselves for manufacturing excellence.
Remember that the right equipment is just the beginning—proper implementation, operator training, and ongoing optimization are equally important to successful aerogel production. Partner with vendors who understand these requirements and can provide appropriate support throughout your aerogel manufacturing journey.
Ready to transform your aerogel production capabilities? Contact our team of specialists at Aerogel Machinery LLC to discuss your specific requirements and discover how our purpose-built, turnkey aerogel production solutions and systems can help you achieve consistent, high-quality aerogel production with maximum efficiency.
What equipment is needed for a complete aerogel production line?
Forget conventional production thinking. A complete aerogel production line requires four critical system categories: sol-gel preparation equipment (temperature-controlled reactors with precision mixing), aging vessels (for network strengthening), drying systems (the heart of your operation), and quality control instrumentation. Most manufacturers underestimate the importance of integrated control systems—yet they’re what separates amateur setups from professional operations. Your production ambitions will determine whether you need laboratory-scale equipment (1-2,000mL) or industrial systems (50-3,000L). Remember: the world’s best aerogel formula is worthless without equipment that can consistently reproduce it.
How much does it cost to set up an aerogel manufacturing facility?
The price of entry varies dramatically with your ambitions. Laboratory-scale aerogel equipment starts around 10,000−10,000−30,000 for commercial systems, while industrial production lines require 500,000
−500,000−5 million investment. But here’s what others won’t tell you: the equipment is just the beginning. Factor in specialized facility modifications (30-50% of equipment costs), ongoing operational expenses (energy, materials, maintenance), and labor. The good news? Recent innovations in supercritical drying equipment have reduced production costs by up to 70%. The pioneers who invest strategically today are positioning themselves to capture tomorrow’s growing aerogel market.
What is the most efficient aerogel production method for commercial applications?
Efficiency isn’t one-size-fits-all in aerogel production. The method that transforms your operation depends on your specific requirements. For premium thermal insulation (0.012-0.018 W/m·K), supercritical CO₂ drying remains the gold standard—now with 40-60% better energy efficiency through advanced recovery systems. Cost-sensitive applications? Consider ambient pressure drying with its 30-40% lower investment requirements. The true manufacturing pioneer recognizes that hybrid approaches often deliver the best economics. Want the ultimate efficiency breakthrough? Roll-to-roll continuous processing increases throughput by 300-400% for aerogel blankets, revolutionizing production economics.
Can aerogel production be scaled from laboratory to industrial level?
Scaling isn’t simply about bigger equipment. The journey from laboratory to industrial aerogel production challenges even experienced manufacturers. What works perfectly in a 1L reactor often behaves differently in a 1,000L vessel. The pioneers who succeed employ a stepped scaling approach, using pilot-scale equipment (20-50L) as their proving ground before full industrial implementation. The critical question isn’t “Can we make more?”—it’s “Can we maintain precise parameter consistency at scale?” Choose aerogel production systems with demonstrated scale-up success and computational modeling capabilities. Your industrial ambitions deserve equipment that grows with your expertise.
What safety systems are required for aerogel manufacturing equipment?
Safety isn’t an add-on—it’s foundational to successful aerogel production. Your equipment must include certified pressure vessels, redundant pressure relief systems, emergency shutdowns, and continuous monitoring with automated alerts. Don’t compromise on explosion-proof electrical classifications and proper ventilation systems (6-12 air changes hourly) when handling flammable solvents. These systems represent 15-20% of equipment costs but are non-negotiable. The true manufacturing pioneer knows that comprehensive safety documentation and regular personnel training aren’t just regulatory requirements—they’re the foundation of operational excellence that distinguishes leaders from followers in silica aerogel manufacturing equipment.
Leave a Reply