
You’ve heard about aerogel – the ‘frozen smoke’ that seems to defy physics. It’s incredibly light yet unbelievably insulating.
But how do you actually make the stuff, especially in a practical, usable form like aerogel felt?
It’s no-magic, but rather a precise manufacturing process grounded in chemistry and engineering. We made is guide to cut through the complexity. We’ll walk you through the entire silica aerogel felt production journey, step-by-step.
From the foundational sol-gel reactions that build the nanostructure, to the make-or-break drying stage, and the crucial fiber reinforcement techniques – it’s all here. You’ll see how raw materials transform into high-performance insulation blankets.
Think of this as your blueprint to understanding – and eventually mastering – the aerogel manufacturing process. Let’s break it down.
Key Takeaways
- The production of silica aerogel felts combines sophisticated nanomaterial science with practical manufacturing methods to create the world’s most efficient thermal insulation materials. While traditional supercritical drying offers the best performance, newer ambient pressure techniques dramatically reduce costs without significantly compromising thermal properties. Successful commercial products balance precise sol-gel chemistry, appropriate drying methods, and effective fiber reinforcement to achieve both thermal efficiency and mechanical durability.
Table of Contents
Why Aerogel Felts Are Revolutionary Insulation Materials
The material you’re about to learn about defies conventional physics.
Imagine holding a solid that’s 99% empty space, feels nearly weightless in your hand, yet can block heat transfer better than almost any substance on earth. This isn’t science fiction—it’s aerogel technology.
The transformation of this remarkable material from research curiosity to commercial insulation product requires mastering a delicate balance of chemistry, physics, and materials engineering. This comprehensive guide examines the silica aerogel felt manufacturing process from molecular precursors to finished insulation blankets.
What makes aerogel production so fascinating is the precise choreography required between chemical reactions and physical transformations. One misstep in the process flow creates collapse, shrinkage, or brittleness—rendering the material useless. But when executed correctly, the result is an insulation material with performance capabilities that conventional materials simply cannot match.
Let’s explore how these remarkable materials are made.
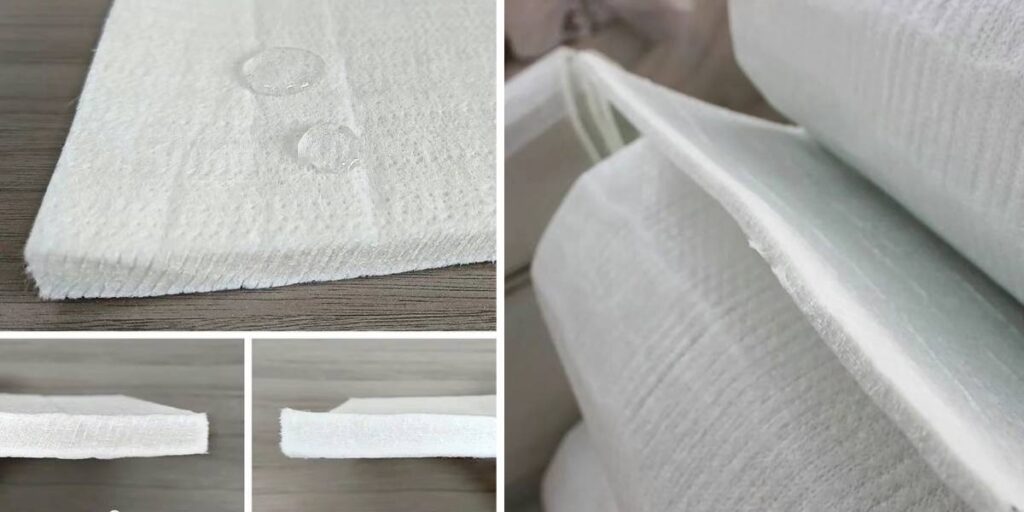
The Science Behind Silica Aerogels: Properties & Benefits
What Makes Aerogels Different From Everything Else
Aerogel is not a specific material but rather a state of matter produced by replacing the liquid component of a gel with gas while preserving the original solid network structure [A Special Material or a New State of Matter]. This unique preparation process creates materials with extraordinary properties:
- Extremely low density: Typically less than 0.1 g/cm³, some less than four times the density of air [Exploring the Versatility of Aerogels]
- Ultra-high porosity: Usually greater than 90%, up to 99.8% [Exploring the Versatility of Aerogels]
- Enormous specific surface area: Ranging from approximately 100-1600 m²/g [Exploring the Versatility of Aerogels]
- Nanoscale pore structure: Pore sizes typically between 5-100 nm [Silica Aerogels for Water Splitting]
- Ultra-low thermal conductivity: Around 0.012-0.04 W/(m·K) at room temperature [A Special Material or a New State of Matter]
Silica (SiO2) aerogel is the most common and extensively studied type, with its framework consisting of interconnected silica nanoparticles forming a three-dimensional network through Si-O-Si bonds [Silica Aerogels for Water Splitting].
Why Aerogel Felts Outperform Pure Aerogels
Pure silica aerogels are typically brittle with low mechanical strength [In Situ Hierarchical Polymerization of Aerogel Composites]. This limits their direct application in scenarios requiring flexibility and structural integrity.
This fundamental limitation led to the development of “aerogel felts” or “aerogel blankets“—composite materials combining an aerogel matrix with a flexible, macroscopic reinforcing structure (fiber networks, fabrics, or foams) [Application of silica aerogel in thermal insulation].
The reinforcement framework significantly improves:
- Compressive strength
- Tensile strength
- Flexibility
- Durability
- Fatigue resistance
- Handling properties
- Dust shedding reduction
This transformation from brittle laboratory curiosity to durable engineering material has dramatically expanded the application range of aerogels, especially in thermal insulation for buildings, industrial pipelines, and aerospace [Exploring the Versatility of Aerogels].
The Five Essential Production Steps
The transformation from liquid precursors to solid aerogel felt follows a sequence of critical steps:
- Gel Preparation: Using the Sol-Gel method, where precursor molecules transform into a sol (colloidal suspension) through chemical reactions, subsequently forming a wet gel with a liquid-filled three-dimensional network structure [Aerogel – Wikipedia].
- Aging: The wet gel strengthens its network structure during a period of rest in its mother liquor or specific solution [An Updated Overview of Silica Aerogel-Based Nanomaterials].
- Fiber Integration: Incorporating reinforcement into the aerogel matrix before, during, or after gelation [Method for producing silica aerogel blanket].
- Drying: The most critical step—replacing liquid in the gel pores with gas while preserving the porous structure. Key techniques include Supercritical Drying (SCD) and Ambient Pressure Drying (APD) [Aerogel – Wikipedia].
- Surface Modification: Often performed to render the aerogel hydrophobic or add specific properties [Preparation of Silica Aerogels by Ambient Pressure Drying].
Now let’s examine each of these production steps in detail.
Mastering the Sol-Gel Process: How Aerogels Form
You cannot create exceptional aerogels without mastering sol-gel chemistry.
This process forms the molecular foundation upon which all subsequent steps depend. The quality of your final aerogel felt is predetermined here, at the very beginning.
How Hydrolysis and Condensation Build Nanostructures
The sol-gel process converts molecular precursors into a colloidal suspension (sol), followed by interconnection of sol particles to form a continuous three-dimensional network (gel) [A Special Material or a New State of Matter].
For silica aerogels, this happens through two key chemical reactions:
- Hydrolysis: Alkoxy groups in silicon alkoxide molecules react with water to form silanol groups (Si-OH). Si(OR)4+nH2O→Si(OR)4−n(OH)n+nROH
- Condensation: The generated silanol groups react with each other or with unhydrolyzed alkoxy groups, eliminating water or alcohol molecules to form siloxane bridges (Si-O-Si). (OH)3Si−OH+HO−Si(OH)3→(OH)3Si−O−Si(OH)3+H2O (Water Condensation), (OH)3Si−OR+HO−Si(OH)3→(OH)3Si−O−Si(OH)3+ROH (Alcohol Condensation)
Through these reactions, nanoscale primary silica particles form and gradually connect, eventually creating a solvent-filled gel network [An Updated Overview of Silica Aerogel-Based Nanomaterials].
The relative rates of hydrolysis and condensation have a decisive impact on the final aerogel’s microstructure (particle size, pore distribution, network connectivity) [A Special Material or a New State of Matter]. For example, higher hydrolysis rates favor more nucleation sites, while lower condensation rates help control particle growth.
This isn’t merely a precipitation reaction—it’s a precisely controlled self-assembly process at the nanoscale that determines the macroscopic properties of your final product.
Choosing the Right Precursor Materials
The choice of silica source defines both your process economics and material properties.
Silicon Alkoxides: The Gold Standard with a Price
Silicon alkoxides, particularly tetraethoxysilane (TEOS) and tetramethoxysilane (TMOS), are the most widely used precursors [Aerogel – Wikipedia]. They offer high reactivity and relatively simple chemical properties.
Since these compounds are typically non-polar liquids immiscible with water, a co-solvent like ethanol or acetone is usually added to form a homogeneous solution [Aerogel – Wikipedia].
Drawbacks: They are expensive, and their vapors pose potential health risks, as inhalation can lead to hydrolysis forming nanoparticles in moist tissues like the lungs [Silica Aerogel – Aerogel.org].
Water Glass: The Budget-Friendly Alternative
Water glass (sodium silicate solution) offers a low-cost alternative silicon source [Synthesis of silica aerogel blanket using water glass].
Research has utilized industrial waste (like coal gangue [Ambient-Dried Silica Aerogel Powders from Coal Gangue]) or biomass ash (like bamboo leaf ash) to prepare water glass as a precursor.
Being inherently alkaline, water glass requires acidification or ion exchange to neutralize the alkalinity before it can undergo the necessary reactions [Synthesis of silica aerogel blanket using water glass].
Advantage: Significant reduction in raw material cost.
Disadvantage: Potential presence of impurity ions affecting the final aerogel’s purity and properties [Silica Aerogel – Aerogel.org].
Hybrid Precursors: Built-In Performance Enhancement
To improve specific aerogel properties like hydrophobicity or mechanical strength, manufacturers often use hybrid precursors—blending silanes with organic functional groups (like methyltrimethoxysilane MTMS or methyltriethoxysilane MTES) with traditional tetra-functional silanes [Preparation of MTMS/TEOS co-precursor silica aerogel].
These molecules contain non-hydrolyzable organic groups like methyl (-CH_3), which get incorporated into the final silica network. This organic modification can impart inherent hydrophobicity and potentially eliminate the need for subsequent surface modification steps [Preparation of MTMS/TEOS co-precursor silica aerogel].
The presence of organic groups might enhance network flexibility and mechanical strength while improving thermal stability [Cast-in-place, ambiently-dried, silica insulation].
Feature | Silicon Alkoxides (TEOS, TMOS) | Water Glass (Sodium Silicate) | Fumed Silica (+ Binder) | Hybrid Precursors (e.g., TEOS+MTMS) |
Starting Form | Molecular Liquid | Aqueous Solution | Solid Nanoparticles | Molecular Liquid |
Core Chemistry | Hydrolysis & Condensation | Acidification -> Hydrolysis & Condensation | Dispersion -> Binding/Curing | Hydrolysis & Condensation |
Cost | High [Silica Aerogel – Aerogel.org] | Low [Synthesis of silica aerogel blanket using water glass] | Potentially Lower (commodity material) [Fabrication from fumed silica slurry] | Medium-High |
Purity/Control | High Purity, Good Control [An Updated Overview of Silica Aerogel-Based Nanomaterials] | May contain impurities, Different control [Silica Aerogel – Aerogel.org] | Depends on raw powder, binder control | Good Control, Customizable properties [Preparation of MTMS/TEOS co-precursor silica aerogel] |
Main Advantages | Versatile, High Purity | Low Cost, Potential waste utilization [Ambient-Dried Silica Aerogel Powders from Coal Gangue] | Simplified chemistry, potential cost reduction [Fabrication from fumed silica slurry] | Customizable properties (e.g., hydrophobicity) [Preparation of MTMS/TEOS co-precursor silica aerogel] |
How Catalysts Shape Your Aerogel Structure
Catalysts are not passive participants—they actively shape your aerogel’s microscopic structure.
- Acid Catalysis (e.g., HCl, oxalic acid): Creates faster hydrolysis but slower condensation, producing less branched polymer chains, smaller primary particles, and microporous structures. Acid-catalyzed gelation typically takes longer [A Special Material or a New State of Matter].
- Base Catalysis (e.g., NH₄OH, NaOH): Results in slower hydrolysis but faster condensation, favoring particle growth and aggregation. This tends to form more spherical, larger primary particles with a broader pore size distribution. Gelation time is usually shorter, and the resulting aerogels often have higher transparency and less drying shrinkage [Aerogel – Wikipedia].
- Two-Step Acid-Base Catalysis: This sophisticated approach first initiates hydrolysis under acidic conditions, then adds a basic catalyst to accelerate subsequent condensation. This method better decouples nucleation and growth processes, enabling finer control over the network structure and potentially producing ultra-light aerogels with significantly shorter gelation times [A Special Material or a New State of Matter].
Your choice of catalyst directly impacts particle size, branching degree, pore distribution, and gelation kinetics—ultimately determining your aerogel’s density, surface area, transparency, mechanical strength, and thermal conductivity.
Why Gel Aging Is Crucial for Strong Aerogels
After initial gelation, the wet gel’s network structure is not yet robust enough for the stresses of drying.
Aging (Syneresis) involves letting the wet gel stand in its mother liquor or a specific solvent for a period [An Updated Overview of Silica Aerogel-Based Nanomaterials]. During this time, three important processes occur:
- Continued Condensation: Residual silanol groups continue forming Si-O-Si linkages, enhancing network connectivity strength.
- Dissolution and Reprecipitation (Ostwald Ripening): Smaller silica particles dissolve and reprecipitate onto larger particles or neck regions, strengthening connecting points between particles.
- Shrinkage: As the network cross-links and rearranges, some contraction occurs, expelling part of the pore liquid.
The primary purpose is to enhance the mechanical strength of the gel skeleton to better withstand capillary pressures during subsequent drying [An Introduction to Sol-Gel Processing for Aerogels]. This is particularly crucial for ambient pressure drying.
Aging is not a passive waiting period but an active stage where the gel network undergoes self-optimization and strengthening—providing another control point for tailoring the final aerogel’s properties.
Critical Drying Methods That Preserve Nanostructure
Here lies the greatest challenge in aerogel production.
Converting a liquid-filled gel into a dry solid while preserving its delicate nanostructure requires overcoming fundamental physical limitations. How you approach this step determines not only your product’s performance but also your manufacturing economics.
The Problem: How Capillary Pressure Destroys Aerogels
If liquid in a wet gel simply evaporates under ambient conditions, the surface tension creates enormous capillary pressure as the liquid-gas interface recedes within nanoscale pores [Aerogel – Wikipedia].
This pressure overpowers the fragile nanonetwork structure, causing irreversible pore collapse and severe shrinkage [Preparation of Silica Aerogels by Ambient Pressure Drying]. The result? A dense xerogel with reduced porosity rather than an aerogel.
Special drying techniques must be employed to avoid or overcome these destructive capillary forces.
Supercritical Drying: The Premium Performance Method
Supercritical drying remains the most effective method for preparing aerogels, first developed by Kistler in 1931 [Aerogel – Wikipedia].
The principle is elegant: avoid the liquid-gas interface entirely. By heating and pressurizing the solvent above its critical point, it transforms into a supercritical fluid where the properties of liquid and gas become indistinguishable [Aerogel – Wikipedia]. In this state, surface tension drops to zero [Polymer/Carbon-Based Hybrid Aerogels].
By slowly reducing pressure, the supercritical fluid transforms directly into gas without generating capillary forces, preserving the gel’s network structure intact [Supercritical Drying – Aerogel.org].
Two common methods exist:
- High-Temperature Supercritical Drying: Uses the original solvent (like ethanol) for supercritical drying. For ethanol, the critical point is approximately Tc=241∘C, Pc=6.1MPa. This method requires high-temperature and high-pressure conditions [Aerogel – Wikipedia].
- Low-Temperature Supercritical CO₂ Drying: A safer, more common method. First, the original solvent in the wet gel is replaced with liquid carbon dioxide through solvent exchange. Then, the system is heated and pressurized above CO₂’s critical point (Tc≈31∘C, Pc≈7.4MPa). Since these conditions are milder, the required operating parameters are significantly reduced [Aerogel – Wikipedia].
Advantages: Best preservation of fine porous structure, minimal shrinkage, highest porosity and surface area [Aerogel – Wikipedia].
Disadvantages: Expensive equipment, high energy consumption, long cycles, difficult scaling, and safety risks [Aerogel – Wikipedia]. Pure aerogels produced this way typically have poor mechanical properties [High Compression Strength Silica Aerogel Monolith].
Ambient Pressure Drying: The Cost-Effective Approach
Ambient pressure drying refers to drying wet gels under normal atmospheric pressure conditions [Preparation of Silica Aerogels by Ambient Pressure Drying]. This approach eliminates expensive pressure equipment, making aerogel production simpler, cheaper, safer, and more scalable.
The key challenge is overcoming capillary pressures without supercritical conditions. Two main strategies are employed:
- Strengthening the Gel Network: Through optimized sol-gel chemistry (using hybrid precursors [Preparation of MTMS/TEOS co-precursor silica aerogel]) or introducing reinforcements (like polymers [High Compression Strength Silica Aerogel Monolith] or fibers [In Situ Hierarchical Polymerization of Aerogel Composites]), the gel network is made strong enough to withstand drying stresses.
- Reducing Capillary Pressure:
- Solvent Exchange: Replacing high surface tension solvents with lower surface tension alternatives (like n-hexane) [Preparation of Silica Aerogels by Ambient Pressure Drying].
- Surface Modification (Silylation): Chemically modifying the gel’s inner surface by replacing hydrophilic silanol groups with non-polar alkylsilyl groups [Preparation of Silica Aerogels by Ambient Pressure Drying]. This reduces liquid-wall interactions, lowers capillary pressure, prevents irreversible condensation during drying, and enables some “spring-back” effect after drying [Cast-in-place, ambiently-dried, silica insulation].
Common silylating agents include trimethylchlorosilane (TMCS), hexamethyldisilazane (HMDS), and hexamethyldisiloxane (HMDSO) [Preparation of Silica Aerogels by Ambient Pressure Drying].
Advantages: Simple equipment, low cost, safe operation, easy scalability [Preparation of Silica Aerogels by Ambient Pressure Drying].
Disadvantages: Greater shrinkage, higher final density, and coarser pore structure than SCD. Requires precise control over solvent exchange and surface modification [High Compression Strength Silica Aerogel Monolith].
Freeze Drying: An Alternative Approach
Freeze drying avoids liquid-phase capillary forces by first freezing the solvent within the gel pores into a solid state, then removing it through sublimation under vacuum [Aerogel – Wikipedia].
While this bypasses capillary pressure, ice crystals formed during freezing can damage the gel’s nanostructure, potentially leading to larger pore sizes [Aerogel – Wikipedia].
Feature | Supercritical Drying (SCD) | Ambient Pressure Drying (APD) | Freeze Drying (Lyophilization) |
Principle | Eliminate L-G interface via supercritical fluid | Strengthen network & reduce capillary pressure via modification | Solid-Gas phase transition (sublimation) |
Conditions | High T&P (solvent SCD) or Mid T & High P (CO₂ SCD) | Ambient P, Elevated T (e.g., 60-150°C) | Low T, Vacuum |
Equipment | Autoclave | Standard oven, ventilation equipment | Freeze dryer, vacuum pump |
Cost/Scalability | High cost, complex, hard to scale [In Situ Hierarchical Polymerization of Aerogel Composites] | Lower cost, simpler, scalable [Preparation of Silica Aerogels by Ambient Pressure Drying] | Medium cost/complexity |
Shrinkage/Density | Minimal shrinkage, lowest density [Silica Aerogel – Aerogel.org] | Medium shrinkage, higher density [High Compression Strength Silica Aerogel Monolith] | Potential damage from ice crystals |
Main Advantages | Best structure preservation | Cost-effective, scalable | Avoids liquid phase |
Main Disadvantages | Cost, complexity, safety [In Situ Hierarchical Polymerization of Aerogel Composites] | Needs complex chemical modification, larger shrinkage [Preparation of Silica Aerogels by Ambient Pressure Drying] | Potential ice crystal damage |
Creating Durable Aerogel Felts: Fiber Reinforcement Techniques
This is where theory meets practical engineering.
Pure aerogels, for all their remarkable thermal properties, cannot survive the real world of handling, vibration, thermal cycling, and mechanical stress. The integration of fiber reinforcement transforms delicate scientific curiosities into robust industrial materials.
How Fibers Transform Brittle Aerogels into Flexible Materials
The core purpose of fiber reinforcement is utilizing high-strength fibers to improve the overall mechanical properties of the composite [Exploring the Versatility of Aerogels]. Fibers form a continuous or semi-continuous skeleton within the aerogel matrix that effectively bear and transfer external loads.
This significantly enhances:
- Compressive strength
- Tensile strength
- Flexural strength
- Impact toughness
- Fatigue resistance
- Handling properties
- Dust shedding reduction
Four Methods to Combine Aerogels with Reinforcements
There are several approaches to combining aerogels with fiber reinforcements:
1. In-situ Gelation in Preformed Fiber Matrices
This widely-used method starts with a porous flexible matrix (non-woven fiber felt, woven fabric, or open-cell polymer foam) that gets impregnated with aerogel precursor sol. After gelation, aging, and drying, the result is an aerogel-filled composite [Method for producing silica aerogel blanket].
Common matrix materials include:
- Glass fibers/wool [Synthesis of silica aerogel blanket using water glass]
- Polyester fibers [Robust Silica–Polyimide Aerogel Blanket]
- Polyimide (PI) foam [Robust Silica–Polyimide Aerogel Blanket]
- Mullite fibers [In Situ Hierarchical Polymerization of Aerogel Composites]
- Carbon fibers [Carbon Fiber—Silica Aerogel Composite]
The main challenge is ensuring uniform sol infiltration throughout the matrix before gelation occurs, particularly in continuous production processes [Method for producing silica aerogel blanket].
2. Direct Fiber Addition to Sol
Another approach disperses short-cut fibers directly into the precursor sol [In Situ Hierarchical Polymerization of Aerogel Composites]. As the sol gels, these dispersed fibers become embedded within the aerogel network. This requires ensuring uniform fiber dispersion and sometimes surface treatment to enhance interfacial bonding [Carbon Fiber—Silica Aerogel Composite].
3. Slurry Impregnation Technique
This alternative starts with pre-formed silica nanoparticles (like fumed silica) mixed with solvents and binders to create a slurry [Fabrication from fumed silica slurry]. A fiber blanket is impregnated with this slurry, cured through heat treatment, and then dried (usually at ambient pressure).
This method potentially simplifies the chemical process, uses commercialized raw materials, lowers costs, and is particularly suitable for ambient pressure drying [Fabrication from fumed silica slurry].
4. Using Pre-made Aerogel Particles
This approach uses pre-prepared aerogel particles/powders mixed with polymers to form coatings or slurries that are applied to fiber surfaces or filled between fiber layers [Synthesis of silica aerogel blanket using water glass].
Successful Commercial Examples
The literature reports numerous successful aerogel felt/blanket preparations:
- Silica-PI aerogel blankets: Prepared by in-situ silica sol-gelation within polyimide foam, followed by hydrophobic modification and ambient pressure drying [Robust Silica–Polyimide Aerogel Blanket].
- Water glass-based aerogel blankets: Using inexpensive water glass with alumina sol-modified glass wool reinforcement [Synthesis of silica aerogel blanket using water glass].
- Fumed silica aerogel blankets: Mixing fumed silica and MTMS to form a slurry, impregnating fiber blankets via roll coating, followed by heat curing and ambient pressure drying [Fabrication from fumed silica slurry].
- Carbon fiber reinforced silica aerogels: Using water glass as the silicon source with surface-modified carbon fibers [Carbon Fiber—Silica Aerogel Composite].
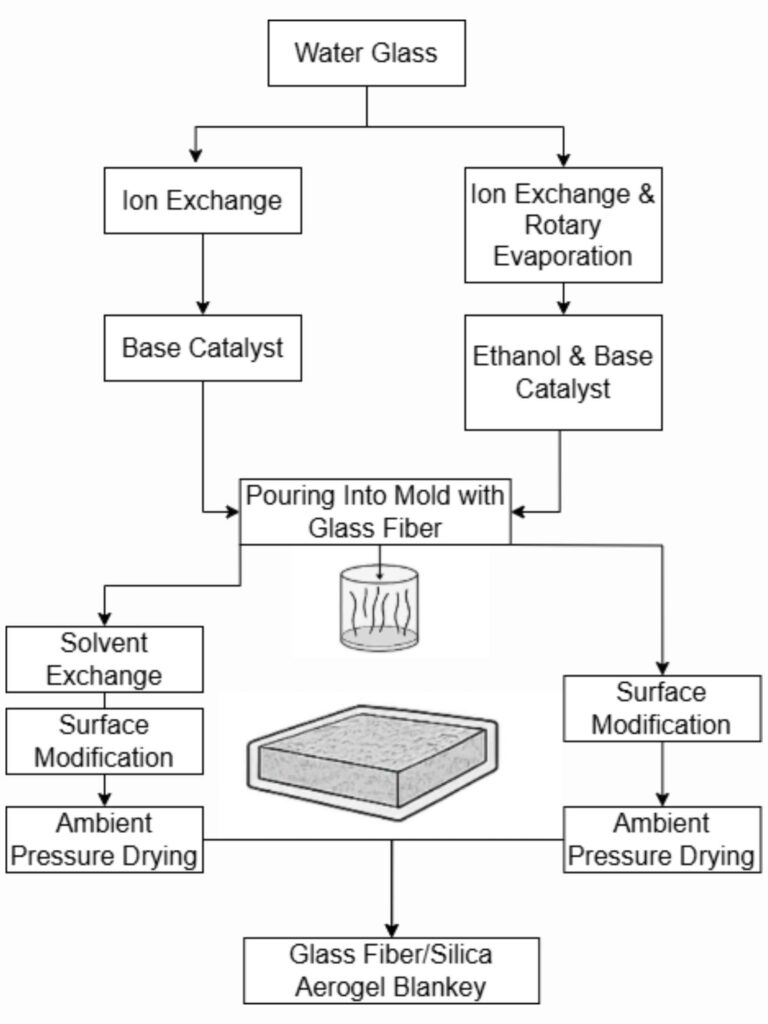
Cost-Effective Production: The Fumed Silica Advantage
Not all paths to aerogel production require molecular precursors.
The fumed silica approach represents a significantly different preparation philosophy—utilizing pre-made nanoparticles as building blocks rather than growing them from molecular seeds.
How Fumed Silica Bypasses Traditional Sol-Gel Chemistry
This method uses commercially available, highly dispersed amorphous silica nanoparticles (fumed silica) as the starting material [Fabrication from fumed silica slurry]. The process typically includes:
- Dispersing fumed silica powder in a suitable solvent to form a stable slurry.
- Adding a binder or cross-linker (like MTMS) to connect the dispersed particles during processing.
- Combining this slurry with fiber reinforcement.
- Inducing the binder reaction through heating to solidify the slurry.
- Drying under ambient pressure.
Step-by-Step Fumed Silica Production Method
A specific implementation [Fabrication from fumed silica slurry]:
- Mix commercial fumed silica and MTMS in water/ethanol to prepare a slurry.
- Impregnate a fiber blanket uniformly using roll coating.
- Heat treat the impregnated blanket to cure the slurry.
- Dry under ambient pressure. Since MTMS introduces hydrophobicity, this may enable ambient pressure drying without additional surface modification or solvent exchange steps.
Pros and Cons of the Fumed Silica Approach
Potential Advantages:
- Simplified Chemistry: Bypasses complex sol-gel reactions, using pre-formed nanoparticles as building blocks.
- Cost Reduction: Fumed silica is a relatively low-cost industrial raw material compared to high-purity silicon alkoxides.
- Process Integration: Well-suited for combination with fiber blankets and ambient pressure drying.
- Shorter Cycle Time: Significantly reduces production cycles compared to traditional sol-gel methods.
Potential Disadvantages:
- Limited Structural Control: The final nanostructure might differ from bottom-up sol-gel construction, with less precise control over pore structure.
- Raw Material Dependence: Performance heavily depends on the characteristics of the fumed silica (particle size, surface area, purity) and binder effectiveness.
- Interfacial Bonding Challenges: Ensuring strong connections between particles and fibers can be difficult.
This “building block” approach simplifies the chemical process and holds considerable potential for cost reduction and production streamlining, especially for thermal insulation blankets using ambient pressure drying.
High-Temperature Performance: Using Opacifiers Effectively
Aerogels excel at room temperature insulation, but maintaining this performance at high temperatures requires addressing radiative heat transfer.
Why Standard Aerogels Fail at High Temperatures
Silica is relatively transparent in the infrared spectrum (especially 2-8 μm range) [Enhanced thermal insulation via opacifier integration – CSIC]. As temperatures rise above ~227°C, radiation becomes a significant heat transfer mechanism, accounting for over 30% of total thermal conductivity at high temperatures.
This causes pure silica aerogel’s effective thermal conductivity to rise sharply, degrading insulation performance [Cast-in-place, ambiently-dried, silica insulation]. For high-temperature applications (aerospace, industrial furnaces, high-temperature pipelines), measures must be taken to suppress radiative heat transfer.
How Opacifiers Block Infrared Radiation
Opacifiers block thermal radiation by absorbing and/or scattering infrared radiation [In Situ Hierarchical Polymerization of Aerogel Composites]. They increase the composite material’s extinction coefficient in the infrared range, reducing thermal radiation flux and lowering radiative thermal conductivity at high temperatures [Enhanced thermal insulation via opacifier integration – CSIC].
Six Best Opacifier Materials for Aerogel Composites
Common opacifiers for silica aerogels include:
- Titanium Dioxide (TiO₂) [Cast-in-place, ambiently-dried, silica insulation]
- Silicon Carbide (SiC) [In Situ Hierarchical Polymerization of Aerogel Composites]
- Zirconium Dioxide (ZrO₂) [In Situ Hierarchical Polymerization of Aerogel Composites]
- Carbon-based materials (Carbon Black, Graphene Oxide) [Enhanced thermal insulation via opacifier integration – CSIC]
- Amorphous silica nanoparticles [Enhanced thermal insulation via opacifier integration – CSIC]
- Alumina (Al₂O₃) [Thermal Insulation with Hollow Opacifiers – PMC]
How to Incorporate Opacifiers into Aerogels
Opacifiers are typically added during the sol stage of the sol-gel process, mixed uniformly with the precursor solution. As gelation proceeds, the particles become embedded within the forming aerogel network [Cast-in-place, ambiently-dried, silica insulation].
Achieving uniform dispersion is crucial for optimal opacification. Opacifiers can also be added as fillers to nanofiber aerogels [Ultra-Light Silica Nanofibrous Aerogel with TiO2].
Optimizing Opacifier Performance
The effectiveness of opacifiers depends on multiple factors:
- Size Effect: For each temperature range and radiation wavelength, there’s an optimal particle size that maximizes extinction. For SiC particles, studies suggest the optimal diameter is about 4 μm at T<400 K, whereas at higher temperatures, it’s about 3 μm [Optical properties of opacifier particles in silica aerogels].
- Concentration Trade-off: Increasing opacifier concentration enhances radiation blocking but raises solid-phase thermal conductivity. Most opacifiers (e.g., SiC at ~83.6 W/(m·K) [Thermal Insulation with Hollow Opacifiers – PMC]) have much higher conductivity than the aerogel skeleton itself. Beyond a certain threshold, the increase in solid conductivity may offset the reduction in radiative conductivity.
- New Strategies: To effectively suppress radiation while minimizing negative density impacts, researchers are exploring novel opacifiers like hollow structures. Theoretical studies suggest hollow opacifiers (like hollow SiC microspheres) might achieve lower total thermal conductivity than solid opacifiers [Thermal Insulation with Hollow Opacifiers – ResearchGate].
Key Properties That Determine Aerogel Felt Quality
The ultimate goal of all these production decisions is creating aerogel felt products with specific performance characteristics. Several key properties must be balanced:
Mechanical Properties: Making Aerogels Tough Enough for Real Use
A significant drawback of pure silica aerogel is its brittleness and low mechanical strength [Exploring the Versatility of Aerogels]. Fiber reinforcement dramatically improves flexibility, compressive strength, tensile strength, fatigue resistance, and durability.
For example:
- Mullite fiber-reinforced Al₂O₃-SiO₂ aerogel composites reportedly achieved a compressive strength of 0.41 MPa at 10% strain [In Situ Hierarchical Polymerization of Aerogel Composites].
- Some aerogel monoliths prepared with cyclic olefin siloxane co-oligomers exhibited extremely high compressive strengths (35.7 to 199.3 MPa) [High Compression Strength Silica Aerogel Monolith].
Beyond fiber reinforcement, other strengthening strategies include:
- “Scaffold polymer composite” techniques to enhance inter-particle connections [High Compression Strength Silica Aerogel Monolith]
- Specific precursors that form tougher networks (like MTMS or cyclic olefin siloxane) [Cast-in-place, ambiently-dried, silica insulation]
Thermal Properties: Ultra-Low Conductivity That Outperforms Traditional Insulation
Ultra-low thermal conductivity is the defining advantage of aerogel materials [A Special Material or a New State of Matter].
At room temperature, silica aerogel felts typically achieve thermal conductivity between 0.012 to 0.04 W/(m·K) [Exploring the Versatility of Aerogels]. Optimized structures with TiO₂ opacifiers have been reported with thermal conductivity as low as 0.019 W/(m·K) [Ultra-Light Silica Nanofibrous Aerogel with TiO2].
Thermal conductivity is influenced by temperature, density, pore structure, fiber reinforcement type and content, and opacifier characteristics. Generally, higher density increases solid-phase thermal conduction, while opacifiers reduce radiative heat transfer at high temperatures but may slightly increase room-temperature conductivity [Fabrication from fumed silica slurry].
Hydrophobicity: Essential for Long-Term Performance
Natural silica surfaces are hydrophilic due to numerous silanol groups (-SiOH) [Exploring the Versatility of Aerogels]. Hydrophilic aerogels readily absorb moisture, which dramatically increases thermal conductivity through capillary condensation.
For practical applications in humid environments, aerogel felts must be hydrophobic [Application of silica aerogel in thermal insulation]. This is crucial for both performance stability and successful ambient pressure drying [Preparation of Silica Aerogels by Ambient Pressure Drying].
Hydrophobicity is typically achieved through:
- Surface modification (silylation) during or after gel formation
- Using hybrid precursors that inherently contain hydrophobic groups (like MTMS)
Typical hydrophobic aerogels have water contact angles greater than 140° [Exploring the Versatility of Aerogels].
Cost and Scalability: Making Aerogels Commercially Viable
High production cost has historically limited the widespread commercial application of aerogel technology [Kinetics of Supercritical Drying of Gels]. Costs stem primarily from expensive precursors and energy-intensive drying processes.
To reduce costs and improve production efficiency, several strategies have emerged:
- Using Low-Cost Precursors: Replacing silicon alkoxides with water glass [Synthesis of silica aerogel blanket using water glass], fumed silica [Fabrication from fumed silica slurry], or industrial/agricultural waste as silicon sources.
- Adopting Ambient Pressure Drying: Avoiding high-pressure equipment, simplifying processes, reducing equipment costs, and enabling continuous production [Preparation of Silica Aerogels by Ambient Pressure Drying].
- Process Optimization: Achieving “one-pot” synthesis with hybrid precursors to reduce steps [Preparation of MTMS/TEOS co-precursor silica aerogel], or using techniques like microwave heating to accelerate sol-gel processes.
The commercial viability of aerogel felts depends on balancing thermal performance with mechanical strength, environmental stability, and manufacturing cost.
Future of Aerogel Manufacturing: Trends & Innovations
Two Main Production Approaches
The production paths for silica aerogel felts primarily follow two models:
- Sol-Gel Method + Fiber Integration + Drying: The classic approach using different precursors (silicon alkoxides, water glass, hybrid precursors), drying techniques (SCD or APD), and fiber integration methods.
- Fumed Silica Slurry Method + Fiber Integration + Drying: An alternative route using pre-formed nanoparticles with binders to create slurries that impregnate fiber blankets, followed by curing and drying.
Current Development Trends
Current developments show clear directions:
- Cost-Effectiveness and Scalability: Moving toward lower costs and easier scaling through ambient pressure drying, inexpensive precursors, and continuous production processes.
- Performance Enhancement: Improving mechanical properties while maintaining thermal performance, optimizing opacifiers for high-temperature applications, and adding multifunctionality (flame retardancy [Robust Silica–Polyimide Aerogel Blanket], sound absorption).
Challenges Still Being Addressed
Despite significant progress, several challenges persist:
- Cost: Still relatively high compared to traditional insulation materials, limiting broader market adoption.
- Performance Balance: Achieving optimal mechanical strength without sacrificing thermal conductivity remains a delicate balance.
- Long-Term Durability: Performance stability under real environmental conditions (humidity, heat, mechanical stress, UV radiation) requires further validation [Aerogel-Based Composite Nanomaterials – CORDIS].
- Sustainability: Developing more environmentally friendly production processes and end-of-life considerations [Aerogel-Based Composite Nanomaterials – CORDIS].
Future Research Frontiers
Future research will likely focus on:
- Novel Precursors and Green Chemistry: Exploring more widely available, low-cost, environmentally friendly silicon sources and greener solvents.
- Advanced Reinforcement Strategies: Developing novel fiber materials, optimizing interfacial bonding, and designing gradient or multi-scale reinforcement structures.
- Efficient Opacification: Researching new opacifier materials with higher extinction efficiency, lower density, and better high-temperature stability (like hollow nanoparticles [Thermal Insulation with Hollow Opacifiers – ResearchGate]).
- Process Innovation: Further optimizing ambient pressure drying, developing continuous production lines, and applying computational modeling to guide material design.
- Expanded Applications: Exploring aerogel felts in new fields like flexible electronics, thermal management in energy storage, personal protective equipment, and medical devices [Silica Aerogels for Water Splitting – MDPI].
The production of silica aerogel felts continues to evolve through technological innovation targeting cost, performance, and scalability challenges. As these materials become more accessible and customizable, they will play an increasingly important role in energy conservation, emissions reduction, and advanced materials applications.
Partner With Aerogel Manufacturing Experts
The journey from liquid precursors to finished aerogel felt products combines sophisticated chemistry, precise process control, and advanced materials engineering. As we’ve seen, successful manufacturing requires mastery of sol-gel processes, drying techniques, fiber reinforcement methods, and performance optimization strategies.
The real challenge isn’t just understanding these processes—it’s implementing them at scale while maintaining quality and controlling costs.
This is where Aerogel Machinery LLC comes in.
As specialists in silica aerogel production equipment, we’ve spent years translating complex manufacturing science into reliable, efficient production systems. The depth of technical knowledge demonstrated in this article reflects the same expertise that goes into every piece of equipment we design and build.
Our systems address the key manufacturing challenges outlined in this article:
- Sol-gel preparation systems with precise catalysis control
- Advanced drying equipment for both supercritical and ambient pressure processes
- Fiber integration technology that ensures uniform aerogel distribution
- Process optimization tools that balance thermal performance with mechanical strength
What truly sets Aerogel Machinery apart isn’t just our equipment—it’s our problem-solving approach. We specialize in creating customized solutions that match your specific requirements, from laboratory-scale research systems to full industrial production lines.
Ready to elevate your aerogel manufacturing capabilities? Connect with our team to discuss how our expertise can help you overcome technical barriers and achieve consistent, high-quality production of aerogel felt materials.
The future of thermal insulation is here. Partner with the experts who understand the science behind the solutions.
What is the main advantage of aerogel felts over pure aerogels?
Aerogel felts overcome the inherent brittleness of pure silica aerogels by incorporating fiber reinforcements, significantly enhancing mechanical strength, flexibility, and durability. This fiber skeleton improves compressive and tensile strength, reduces dust shedding, and makes the material practical for real-world applications like building insulation and industrial pipelines.
Which drying method is better for commercial aerogel felt production?
Ambient Pressure Drying (APD) is increasingly preferred for commercial production despite causing more shrinkage than Supercritical Drying (SCD). APD offers significantly lower equipment costs, better scalability, safer operation, and compatibility with continuous manufacturing processes, though it requires careful surface modification and network strengthening.
How do opacifiers improve high-temperature performance of aerogel insulation?
Opacifiers like TiO₂, SiC, and ZrO₂ block thermal radiation by absorbing/scattering infrared waves. At temperatures above 227°C, radiation accounts for over 30% of heat transfer through silica aerogels. Adding optimally-sized opacifiers reduces radiative thermal conductivity, maintaining excellent insulation properties at elevated temperatures.
What are the cost-reduction strategies for aerogel felt manufacturing?
Key cost-reduction strategies include: replacing expensive silicon alkoxides with water glass or fumed silica; utilizing industrial waste as silicon sources; adopting ambient pressure drying instead of supercritical drying; implementing continuous production processes; and developing “one-pot” synthesis methods that combine multiple steps.
How does the choice of precursor affect the final aerogel felt properties?
Precursor choice significantly impacts properties and processing. Silicon alkoxides offer high purity but at high cost. Water glass provides cost benefits but may introduce impurities. Hybrid precursors (e.g., MTMS+TEOS) enable inherent hydrophobicity. Fumed silica offers simplified processing and potential cost reduction but less control over nanostructure.
Leave a Reply